Traditional project delivery doesn’t always cut it—tight deadlines, budget constraints, and unexpected risks can throw a project off track. That’s why many owners turn to alternative delivery methods, which offer more flexibility, better collaboration, and stronger cost control.
But not all methods work the same way. Some speed up construction, while others focus on reducing risk or improving teamwork. This guide breaks down the key alternative project delivery methods, their pros and cons, and when to use them—so you can make the best choice for your next project.
What are Alternative Delivery Methods?
Alternative delivery methods are construction procurement models that go beyond the traditional Design-Bid-Build (DBB) approach. Unlike DBB, where design and construction are separate contracts, these methods integrate planning, design, and construction to improve efficiency, cost control, and risk management.
They are gaining popularity as projects become more complex, requiring faster timelines, collaborative workflows, and innovative risk-sharing models. Industries such as infrastructure, healthcare, and commercial development benefit the most, as they often demand speed, flexibility, and predictable costs to ensure successful project delivery.
Check out this guide on Project Delivery Methods to explore the best options for your next project.
Key Alternative Delivery Methods in Construction Explained
Choosing the right alternative delivery method can significantly impact a project's cost, timeline, and risk management. Unlike traditional method, these methods offer varying levels of collaboration, flexibility, and cost control, depending on the project’s complexity and requirements.
Below, we break down the most widely used alternative construction delivery methods, explaining how each works, its advantages and drawbacks, and when it’s the best fit for your project.
Design-Build (DB)
The Design-Build (DB) method consolidates design and construction under a single contract with one entity—either a design-build firm, contractor-led team, or joint venture. This approach eliminates the traditional separation between designer and contractor, streamlining project execution, reducing conflicts, and allowing construction to begin before design is fully completed.
Pros
- Time Savings: Projects are completed 33% faster than traditional methods.
- Better Collaboration: Unified teams reduce conflicts and align with owner goals.
- Cost Efficiency: Early problem-solving reduces mid-project changes, saving up to 6% in costs compared to traditional delivery methods.
Cons
- Reduced Owner Control: The owner has less direct involvement in design decisions, which can be a drawback for those wanting more control.
- Potential for Limited Competition: Since the design and construction are awarded as a single contract, fewer firms may compete for the project, potentially driving up costs.
- Risk of Over-Dependence: The owner depends heavily on the Design-Build entity, and any issues with their performance can have significant impacts on the project.
Design-Build (DB) Example
Denver International Airport (DEN), one of the busiest airports in the U.S., needed to expand its capacity to accommodate growing passenger demand. The expansion added 39 new gates across three concourses, increasing operational efficiency and passenger flow.
With multiple concourses requiring simultaneous upgrades, the airport authority needed the Design-Build approach to manage design and construction cohesively. The Design-Build approach reduced coordination challenges by consolidating responsibilities under a single contract, minimizing disruptions to ongoing airport operations.
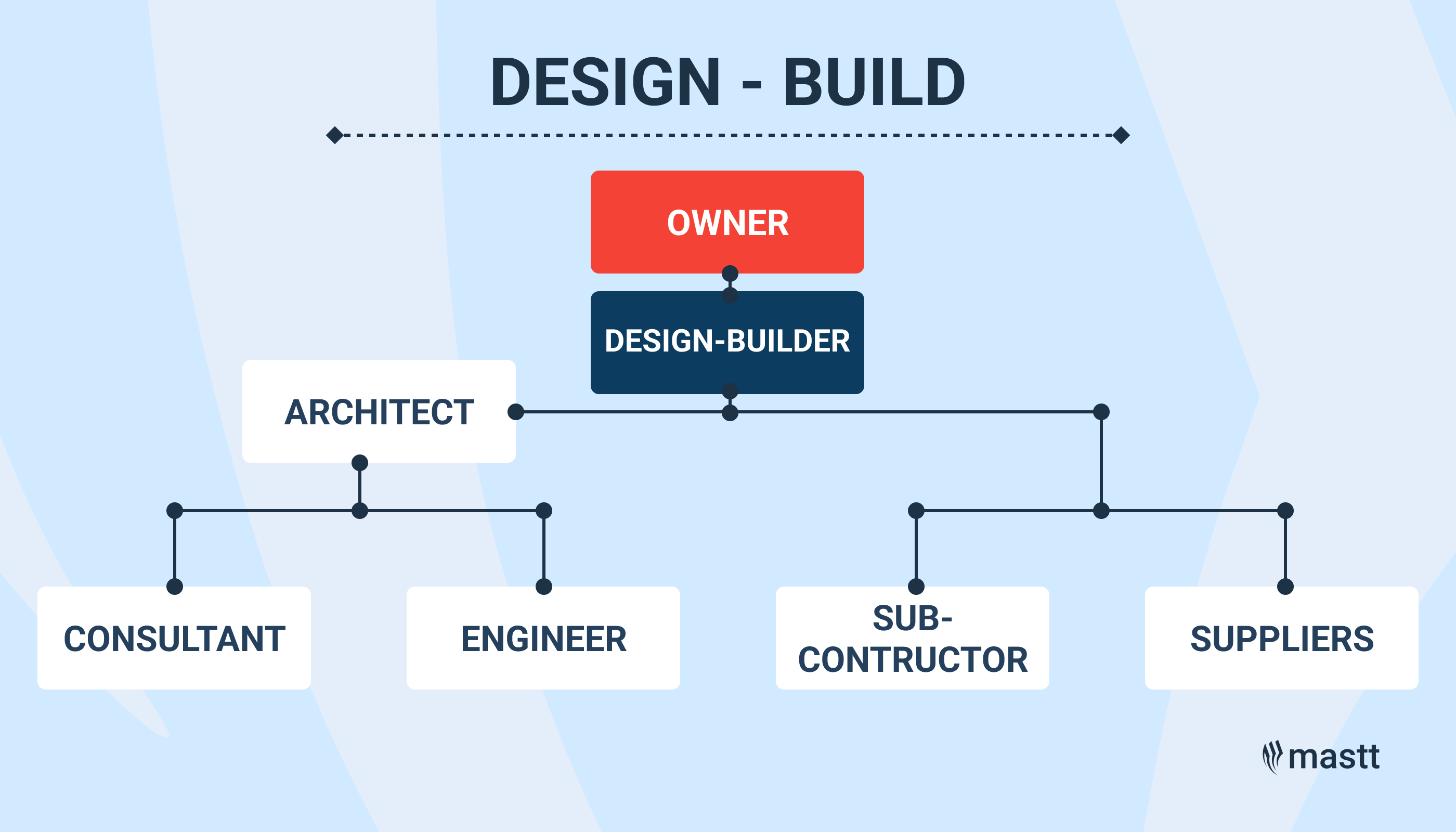
Progressive Design-Build (PDB)
Progressive Design-Build (PDB) follows the same single-entity contract structure as traditional DB but introduces a phased, collaborative approach. The owner selects the design-builder based on qualifications rather than a fixed price, allowing the team to develop the project scope and cost progressively before finalizing the construction contract.
The process has two phases:
Phase 1: Focuses on conceptual design and pre-construction planning, ensuring alignment on scope, budget, and schedule.
Phase 2: Construction begins after the owner approves the design and budget, allowing for adjustments as needed without major disruptions.
Pros
- Greater flexibility to adapt to changes.
- Encourages collaboration and owner involvement.
- Reduces risk of major disruptions during construction.
- Aligns scope, budget, and schedule early.
Cons
- Requires a high level of trust and collaboration between stakeholders.
- May have higher upfront costs during the preconstruction phase.
- Can lead to delays if consensus is not achieved in Phase 1.
- Less suited for projects with rigid budgets or clear initial scopes.
Progressive Design-Build (PDB) Example
The Pure Water San Diego Program is a $5 billion initiative aimed at providing a sustainable and drought-resistant water supply by purifying recycled water. This program will eventually produce nearly half of the city's drinking water by 2035. Phase 1, currently under construction, will deliver 30 million gallons per day of purified water to residents, reducing reliance on imported water sources.
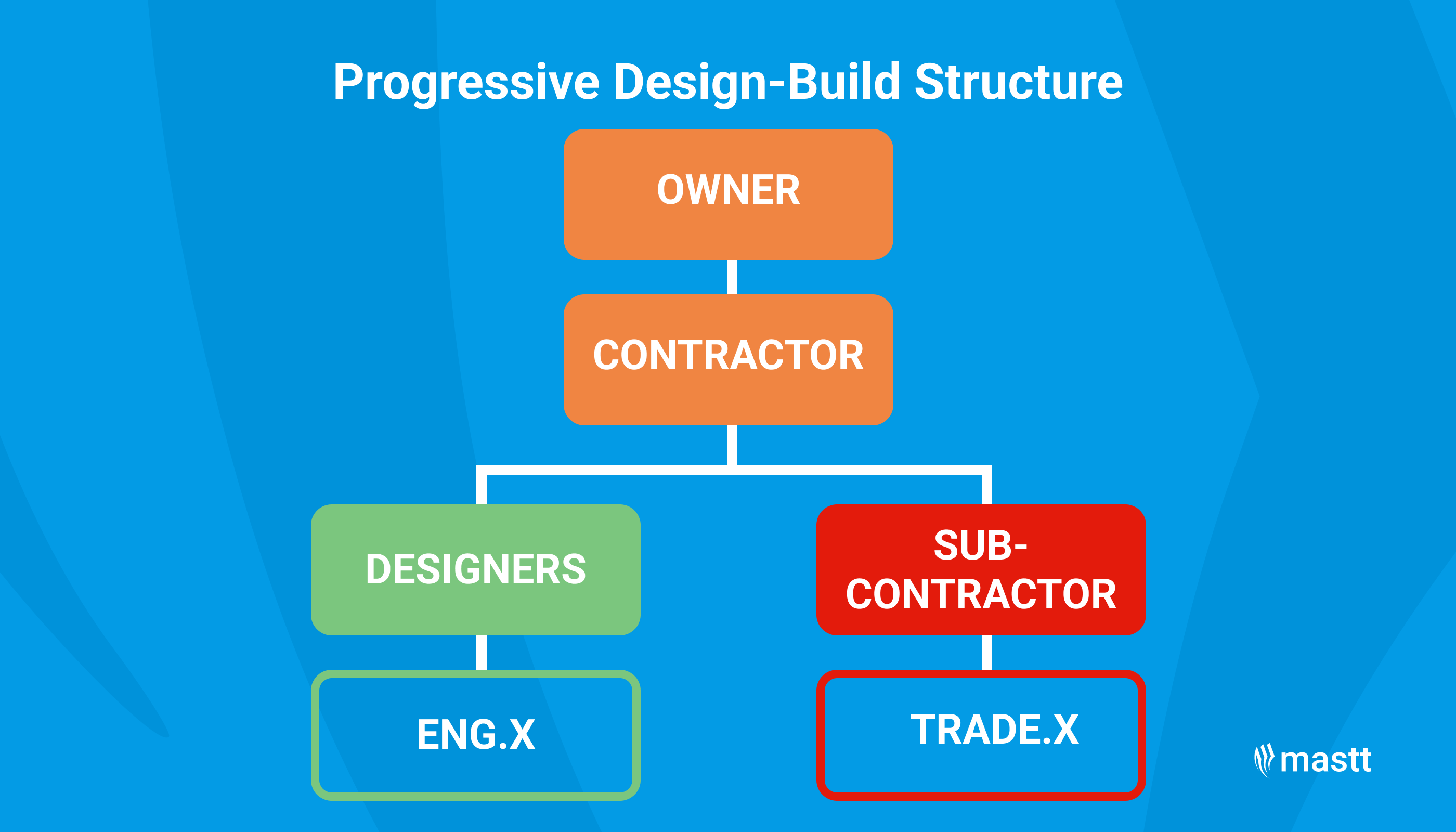
Construction Manager at Risk (CMAR)
The Construction Manager at Risk (CMAR) method involves engaging a Construction Manager (CM) early in the design phase to provide input on constructability, scheduling, and budgeting. The CM later transitions into a contractor role, delivering the project for a Guaranteed Maximum Price (GMP)—shifting cost overrun risks to the CM.
Pros
- Early involvement of the construction manager improves planning and risk management.
- Guaranteed Maximum Price (GMP) ensures cost certainty for the owner.
- Collaboration between the owner, designer, and contractor enhances project outcomes.
- Flexibility to make design adjustments during the pre-construction phase.
Cons
- Requires careful selection of the construction manager to ensure expertise and alignment with project goals.
- The dual role of consultant and contractor could create potential conflicts of interest.
- The owner still assumes some risk if project scope changes or unforeseen issues arise.
CMAR Example
In 2019, the City of Woodbury, Minnesota, faced a water contamination crisis when seven of its 19 wells were found to contain perfluoroalkyl and polyfluoroalkyl substances (PFAS). To ensure a safe drinking water supply, the city needed to design, construct, and commission a temporary water treatment plant within six months—a highly compressed timeline for such a complex project.
Given the urgency and technical challenges of the project, CMAR was chosen to accelerate design and construction while managing risk and cost effectively.
The CMAR firm, Rice Lake Construction Group, worked closely with engineers and city officials from day one to develop a feasible design that could be built within the tight schedule. The project won the 2021 Public Works Project of the Year Award from the American Public Works Association in the Disaster or Emergency Construction Repair ($5M - $25M) category.
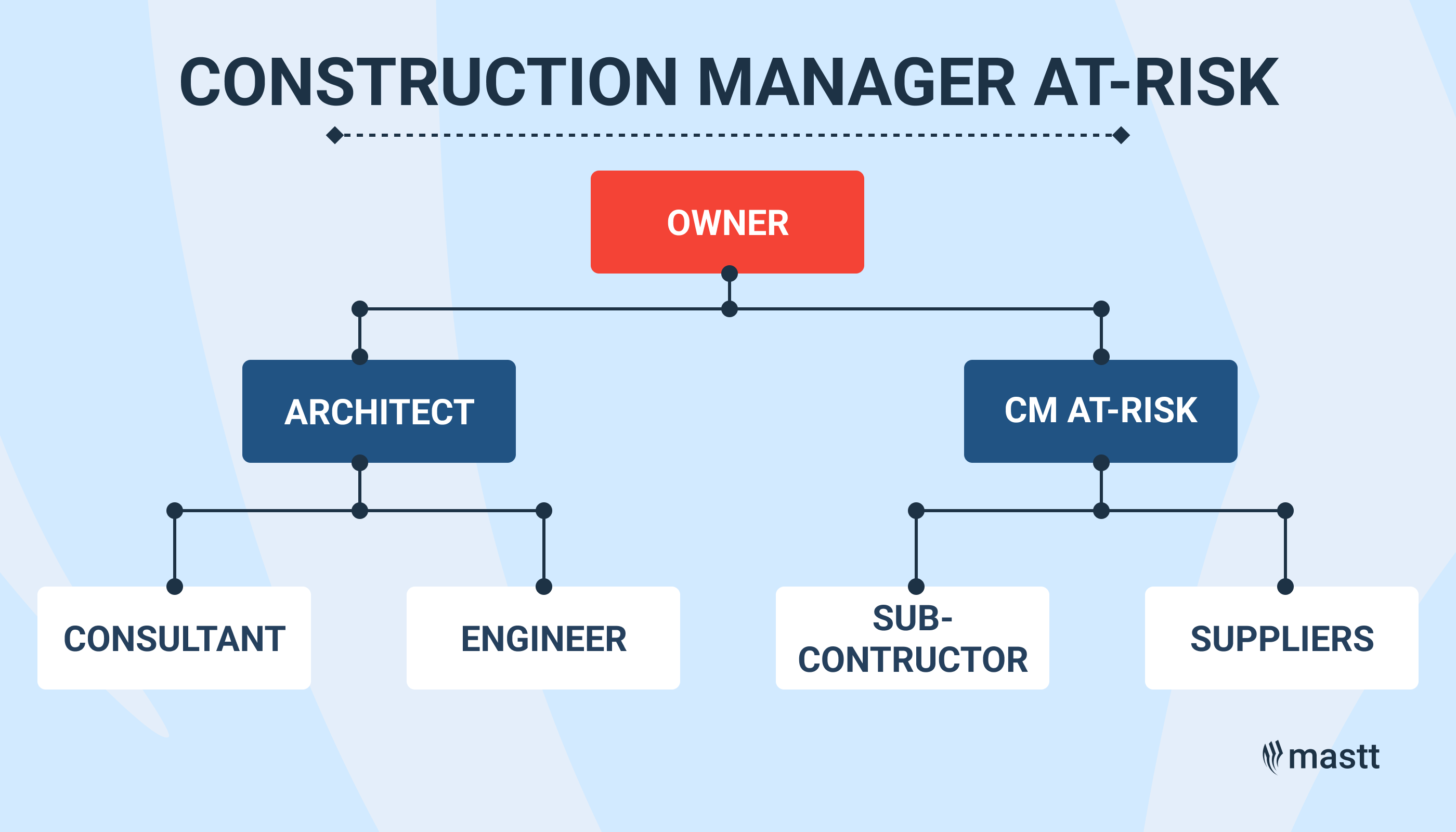
Construction Manager/General Contractor (CMGC)
CMGC delivery method is similar to CMAR but is commonly used for public infrastructure projects. The owner hires a Construction Manager (CM) during the design phase, and once the design is sufficiently advanced, the CM negotiates a contract to act as the General Contractor (GC) for construction.
Pros
- Reduces design errors and delays.
- Increases scheduling flexibility.
- Ensures cost-effective designs.
- Enables selection of skilled contractors for quality results.
Cons
- Requires strong coordination between stakeholders.
- May increase upfront costs.
- Relies heavily on contractor and design team expertise.
CMGC Example
The California Department of Transportation (Caltrans) launched a CMGC pilot program for six major transportation projects, aiming to improve efficiency and cost control. With CMGC, Caltrans remained the engineer of record while engaging a contractor early in the design phase to provide constructability reviews, cost assessments, and scheduling insights. This two-step process allowed the contractor to transition from construction manager to general contractor once a negotiated construction price was agreed upon.
Public-Private Partnerships (PPPs)
In a Public-Private Partnership (PPP or P3), a private entity enters a long-term agreement with a government agency to finance, design, build, operate, and/or maintain public infrastructure. The private sector takes on a significant portion of the risk while receiving returns through user fees, tolls, or availability payments.
Pros
- Access to private sector expertise and innovation.
- Shared financial responsibility enables critical infrastructure development.
- Performance-based accountability ensures high-quality results.
Cons
- Contract complexity can lead to delays and cost overruns.
- Public opposition may arise if user fees or tolls are involved, requiring transparency and communication to build trust.
PPPs Example
P3s has been instrumental in delivering some of the world’s most iconic infrastructure projects. One well-known example is London’s Crossrail project, a massive rail network expansion partially funded and delivered through PPP agreements. The partnership enabled the project to access private capital while maintaining public oversight.
In the U.S., the Long Beach Courthouse in California is another successful example. Delivered under a PPP model, the courthouse was completed on time and within budget. The private partner not only designed and built the facility but also manages its maintenance under a long-term agreement.
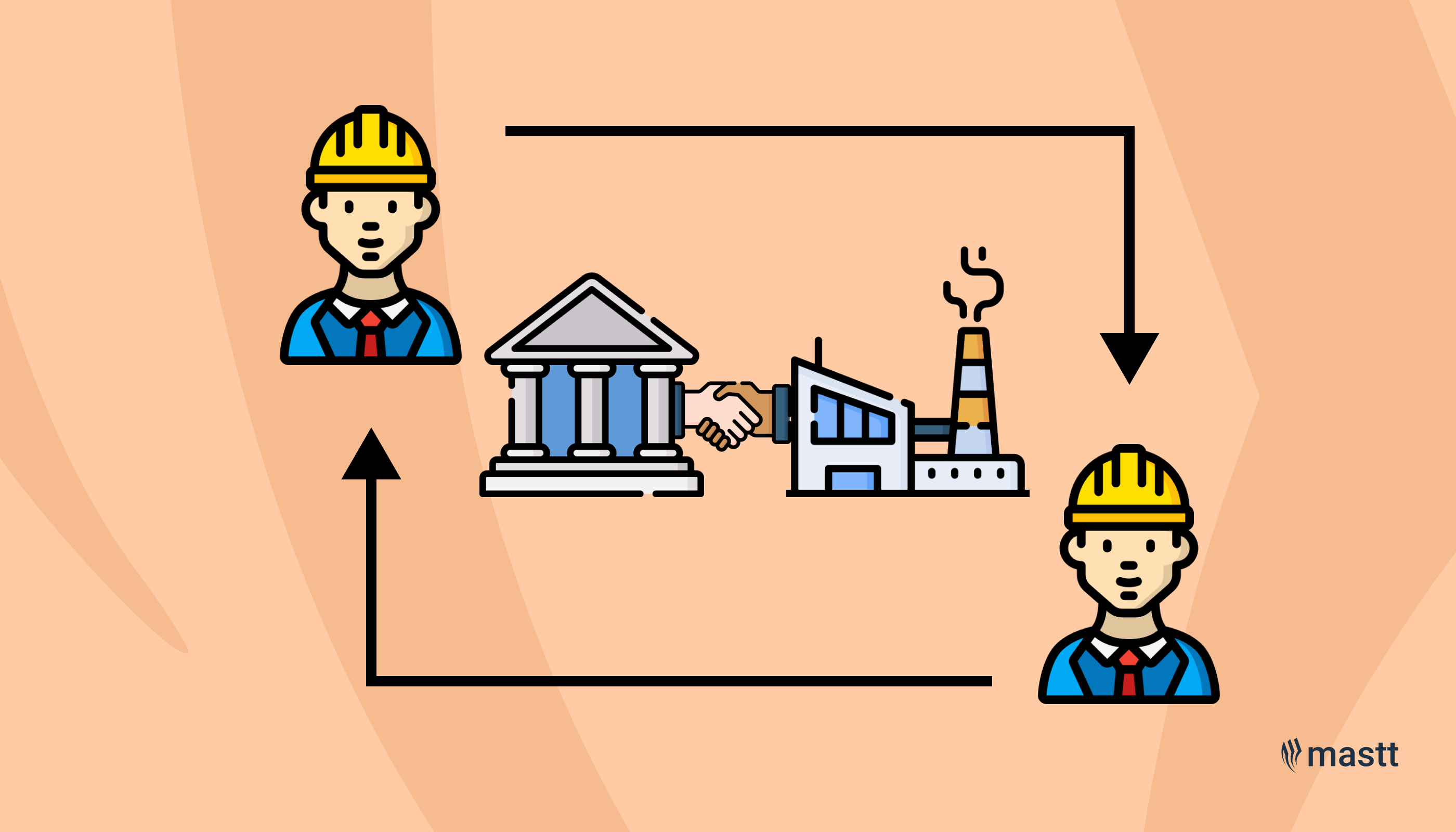
Job Order Contracting (JOC)
Job Order Contracting is a delivery method where an owner awards a multi-year contract to a single contractor for small-to-mid-sized projects without separate competitive bidding for each job. Instead, pre-established unit prices define the cost of various construction tasks, allowing for quick work authorization.
Pros
- Streamlined Procurement: Faster project timelines and reduced administrative overhead.
- Cost Predictability: Pre-priced tasks improve budgeting accuracy and reduce unexpected expenses.
- Efficiency: Studies show JOC can reduce costs by up to 15% compared to traditional methods.
Cons
- Catalog Creation: Developing a comprehensive pricing catalog requires significant upfront effort.
- Limited Scope: Best suited for routine, small-scale tasks rather than large projects.
- Contractor Quality: Selecting and monitoring contractors is critical to ensure consistent performance.
JOC Example
In December 2021, the University of Denver acquired the Kennedy Mountain Campus, a 720-acre property near Red Feather Lakes, Colorado, with the vision of creating an immersive outdoor learning environment as part of their 4D Experience. To achieve this, the university needed to renovate existing facilities, including seasonal cabins, a dining hall, and an activity center, to meet ADA and university standards.
Given the tight timeline to welcome students by the Fall 2022 quarter, traditional procurement methods were deemed too slow. Instead, the university employed Job Order Contracting (JOC), an efficient construction procurement method. They partnered with Facilities Contracting, Incorporated of Littleton, Colorado, to expedite the renovations. This approach allowed construction to commence promptly, ensuring the campus was ready for students in just five months.
Turnkey Project
A Turnkey project is a fully outsourced construction approach where the contractor is responsible for design, procurement, construction, and sometimes commissioning. The owner simply "turns the key" and takes possession of a fully functional facility at handover.
Pros
- Simplicity: A single contractor manages the entire process, reducing complexity and miscommunication.
- Efficiency: Overlapping design and construction phases speed up delivery.
- Cost Predictability: Budgets are typically locked in at the contract stage, minimizing financial risks.
Cons
- Limited Flexibility: Changes during the project are costly and time-consuming.
- Contractor Dependence: Success hinges on selecting a qualified and reliable contractor.
- Reduced Owner Involvement: Owners have limited input during the process, which may not suit those preferring more control.
Turnkey Project Example
The Dubai Metro is a fully automated, driverless urban rail system designed to alleviate traffic congestion and support Dubai’s rapid urban expansion. The project was executed under a Turnkey Project Delivery model, where the contractor handled every stage—from design and engineering to construction, system integration, and commissioning—ensuring a fully functional system was delivered to the Dubai government upon completion.
The Red Line, the first phase of the metro, was awarded as a $7.6 billion turnkey contract to the Dubai Rapid Link (DURL) Consortium, led by Japan’s Mitsubishi Heavy Industries, along with Obayashi Corporation, Kajima Corporation, and Yapi Merkezi. The consortium was responsible for delivering a fully operational rail system, including station construction, track installation, rolling stock procurement, automated control systems, and extensive testing.
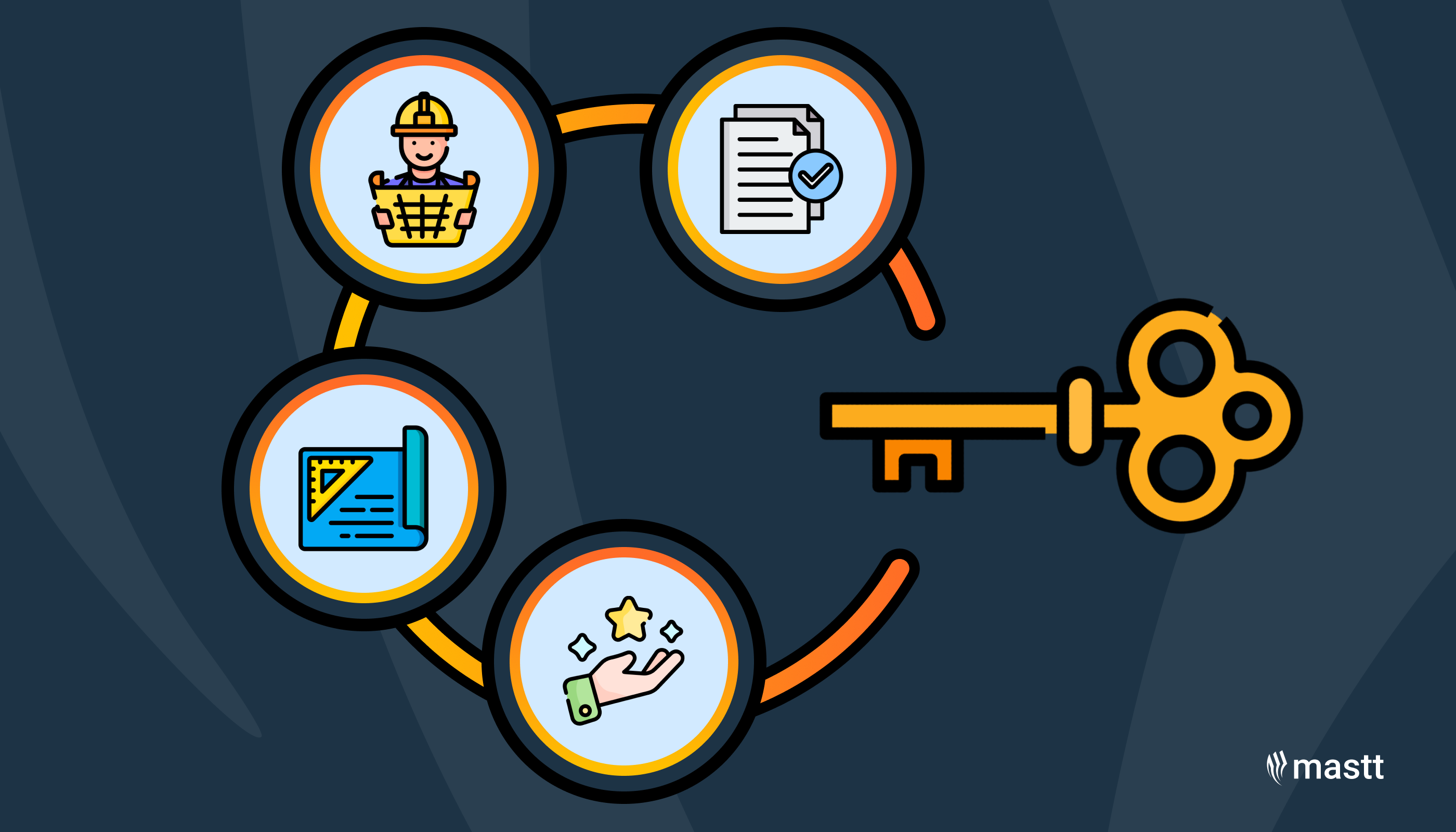
Engineering, Procurement, and Construction (EPC)
EPC is a project delivery model where one firm is responsible for engineering, procurement of materials, and construction. The owner provides general project requirements, and the EPC contractor delivers a fully functional facility.
Pros
- Single Point of Responsibility: The contractor oversees the entire project, simplifying communication and reducing owner risk.
- Cost and Time Control: Well-defined contracts help prevent budget overruns and schedule delays.
- Quality Assurance: Contractors are incentivized to meet high-quality standards to deliver the project successfully.
Cons
- Limited Owner Control: Owners may have less input once the project begins, which could be challenging for those who want more involvement.
- High Dependence on Contractor: The success of the project heavily relies on the expertise and reliability of the contractor.
- Potential for High Initial Costs: Detailed contracts and planning phases may require significant upfront investment.
Variations of EPC
The EPC model has evolved to include variations tailored to specific project needs, such as:
- Engineering, Procurement, and Construction Management (EPCM): The contractor provides management services, while the owner retains control of subcontractors.
- Engineering, Procurement, Construction, Management, and Validation (EPCMV): Adds validation services, often used in regulated industries like pharmaceuticals.
EPC Example
The Tengiz Oil Field expansion, a $48 billion project, aimed to boost production by 260,000 barrels per day, reaching 1 million bpd. Led by Tengizchevroil (TCO), a Chevron, ExxonMobil, KazMunayGas, and Lukoil joint venture, the project used the EPC model to streamline design, procurement, and construction, tackling challenges like high sulfur content and extreme conditions.
By integrating all phases under a single contract, EPC ensured cost control, risk reduction, and timely execution, with production starting in January 2025. This approach reinforced Kazakhstan’s global oil position and showcased EPC’s efficiency in managing complex megaprojects.
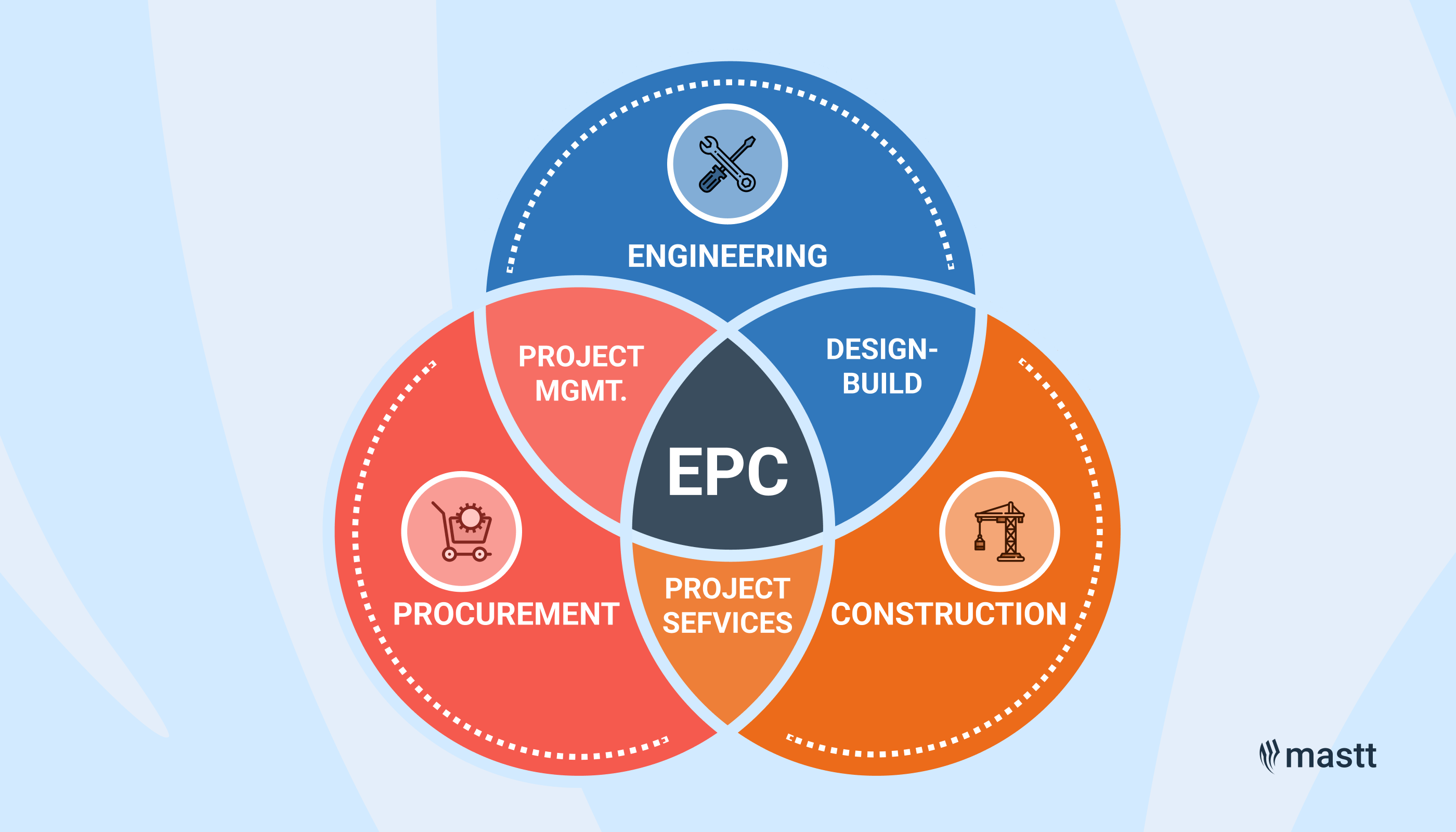
Key Considerations When Choosing an Alternative Delivery Method
Selecting the right alternative delivery method depends on several critical factors. Each project has unique requirements, and choosing the wrong approach can lead to budget overruns, delays, or unnecessary risks. Here’s what to consider before making a decision:
- Project Size & Complexity: Large, multi-phase projects often require integrated, highly collaborative methods like CMAR, CMGC, or PPPs, while smaller, recurring projects benefit from JOC or streamlined approaches like Turnkey.
- Risk Tolerance: Who bears the financial and performance risk? Design-Build and CMAR balance risk between owner and contractor, while EPC and Turnkey models shift most of it to the contractor.
- Budget & Cost Control: If cost certainty is a priority, fixed-price contracts (Turnkey, EPC) may be best. If flexibility is needed, methods like PDB or CMGC allow costs to evolve with the project scope.
- Timeline & Speed: Fast-track methods like DB and PDB enable design and construction to overlap, reducing schedules. P3 and EPC, on the other hand, are structured for long-term infrastructure projects with extended timelines.
- Level of Owner Involvement: Owners who want more control over design and execution often prefer CMAR or CMGC, while those seeking a hands-off approach lean toward Turnkey or EPC, where the contractor takes full responsibility.
Aligning your project goals, risk strategy, and budget priorities with the right delivery method is key to ensuring a successful and efficient construction process.
Final Thoughts on Alternative Project Delivery Methods
Choosing the right alternative delivery method is crucial for controlling costs, managing risk, and ensuring project success. Whether you need speed (DB, PDB), risk management (CMAR, CMGC), or long-term partnerships (PPP, EPC), each method offers distinct advantages.
By aligning your project size, budget, risk tolerance, and timeline with the right approach, you can streamline delivery and improve outcomes. The key is understanding your priorities and selecting a method that best fits your project’s needs.