Labor, materials, equipment, delays, and mistakes all add up to construction costs. If you're managing a build, working on-site, or planning a new project, you're probably looking for clear ways to reduce construction costs without hurting quality or missing deadlines.
That’s exactly what this guide is for. You’ll learn simple, smart steps that help contractors, builders, and project managers lower project costs, avoid waste, control labor and material expenses, and keep every construction project on track.
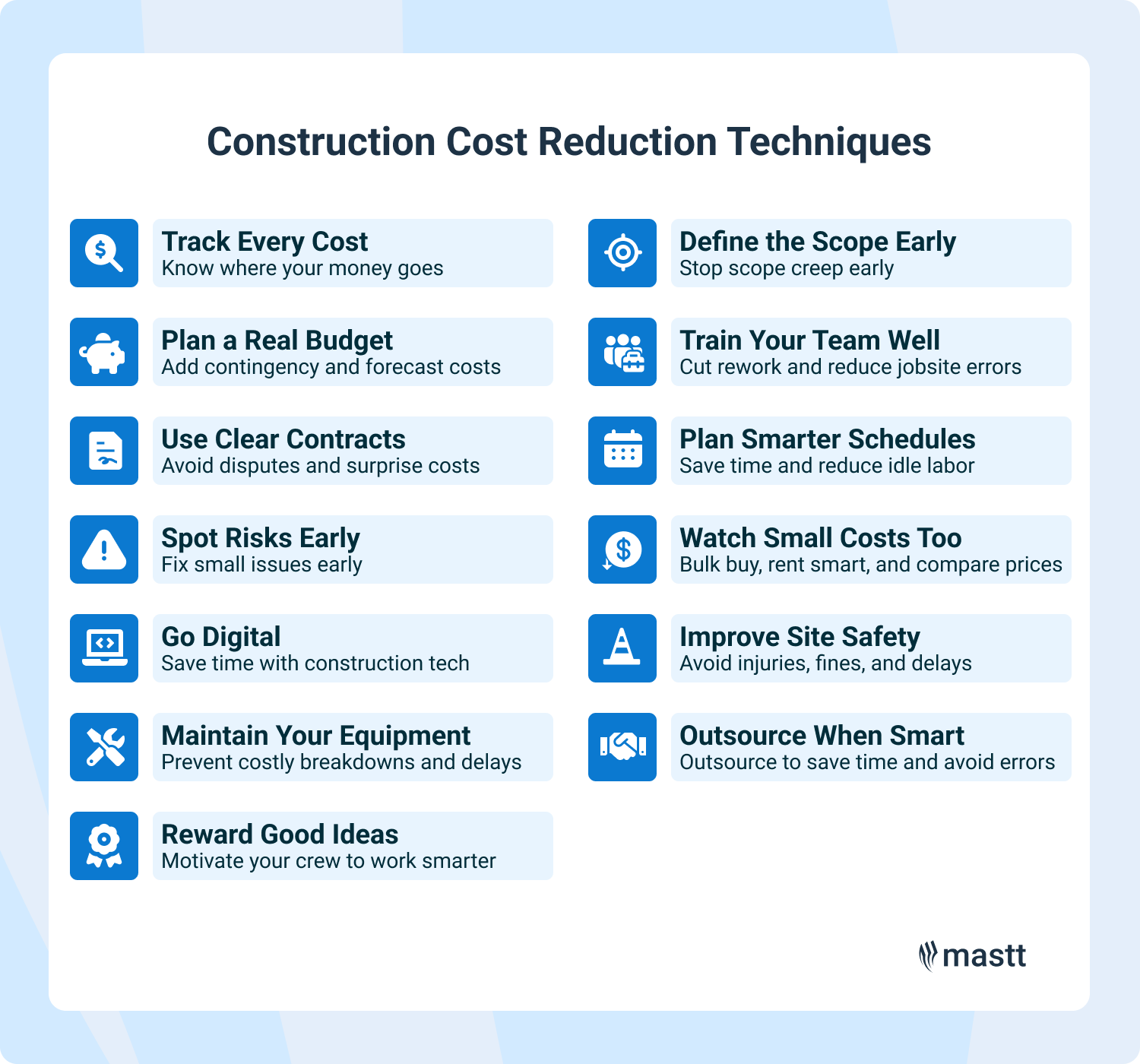
1. Track Project Costs to Find What’s Wasting Your Money
The first step to reducing construction costs is knowing where your money goes. You can’t fix what you don’t see. That’s why tracking every cost (both project costs and overhead) is so important. When you record how much you spend, you can spot budget leaks early and take action before they grow.
Here’s what to track on every construction project:
To make this work, use simple tools like construction cost tracking software, spreadsheets, or mobile apps that work on site. Review costs weekly, not just at the end of the job.
For example, if you notice one project spent 20% more on materials than planned, check why. Did prices increase? Was there a mistake in ordering? Or did waste happen on-site? Once you know the cause, you can fix it before it repeats on the next job.
For a deeper breakdown of how to plan, track, and control spending, check out our full project cost management guide.
2. Set a Clear Project Scope to Avoid Extra Costs
One big reason why construction projects go over budget is scope creep. This happens when extra tasks, changes, or features are added after the project starts without more time or money to match. To avoid this, you need to set a clear project scope from the start and stick to it.
Here’s how to set and manage a clear project scope:
Let’s say your client decides to add another bathroom halfway through the job. If that wasn’t in the original scope, the team now needs more labor, materials, and time—all of which cost money.
But if the scope was clearly defined and agreed on upfront, you’d have the process in place to adjust the timeline and budget properly.
3. Build a Realistic Budget With a Cost Buffer
Many construction projects experience cost overruns because the plan didn’t include enough room for surprises. That’s why every budget should include a cost buffer, also known as a contingency. It gives you flexibility when prices change or unexpected issues come up.
Here’s how to build a more realistic construction budget:
For example, if your labor estimate is $100,000, you might add 10 percent ($10,000) as a buffer. If weather delays the job or material prices jump, that extra money keeps you covered without affecting other parts of the project. It’s much easier to reduce construction costs when your budget plans for what could go wrong, not just what should go right.
4. Train Your Crew to Avoid Costly Mistakes
Construction mistakes cost money, slow down the job, and often lead to rework. Many of these errors happen when workers aren’t fully trained or don’t understand the task clearly. That’s why training your crew is one of the best ways to reduce construction costs and keep projects on track.
Here are simple ways to improve crew training and reduce mistakes:
For instance, if a worker installs flooring the wrong way, the job may need to be redone, costing you extra materials, labor, and time. But if that same task was explained and practiced during training, the mistake could’ve been avoided.
5. Use Strong Contracts to Prevent Disputes and Hidden Costs
Disputes and surprise costs often come from unclear or weak contracts. When terms aren’t clear, changes during the project can lead to arguments, unpaid work, or extra charges.
A strong construction contract helps everyone understand what’s expected, what’s included, and what happens if something changes.
Here’s how to use contracts to control construction costs:
For example, if a contractor adds new work without a signed construction change order, that cost may not be covered or, worse, may be disputed. But with a contract that clearly explains how changes must be approved and priced, both sides stay protected.
6. Schedule Tasks to Save Time and Labor
Wasted time on a job site leads to wasted money. When one task delays another or workers stand idle, your labor costs go up fast. That’s why every construction project needs a schedule that works in the real world, not just on paper.
Here’s how to build a smarter schedule that reduces delays and keeps crews moving:
For example, if electrical work gets pushed but the drywall team still shows up, you now have to reschedule them, possibly at extra cost. But with a solid schedule, crews know exactly when to show up, what needs to be ready, and how long they have.
7. Spot Project Risks Early to Avoid Expensive Delays
Many times, delays are caused by problems that could have been spotted earlier. That’s why one of the smartest ways to reduce construction costs is to find and fix risks before they slow down your project.
Every construction job has risks. You might face weather issues, missing permits, late material deliveries, or even design changes from the client. These problems are common, but they become costly when you don’t plan for them.
Here are the most common risks to watch for and what you can do:
Let’s say you skip checking permit timelines and assume they’ll be approved on time. If the permit is delayed, your entire project might stop, costing you time, crew hours, and extra equipment rental. But if you plan ahead and track approvals closely, you can stay on schedule and avoid paying for lost time.
8. Cut Material and Equipment Costs With Smarter Buying
Most construction projects go over budget because people stick to the same suppliers, order too much, or buy tools they rarely use. Start by planning what you need early. This gives you time to compare prices, check delivery times, and avoid last-minute purchases.
You should also look at what you used on past projects. This helps you avoid waste and spot where you overspent.
Here are simple ways to buy smarter:
Let’s say you always buy framing timber from one seller. If you never check prices elsewhere, you might miss better deals. But if you compare prices every few months, you might find a cheaper option nearby or a better deal for bulk orders.
To quickly estimate labor, materials, and equipment costs, try using our construction cost calculator for accurate budgeting.
9. Use Construction Software to Cut Waste and Speed Up Work
I can’t believe construction teams still rely on spreadsheets, emails, and paper files to manage their projects. Did you know that these tools can slow things down, cause confusion, and lead to costly errors?
A small mistake in a spreadsheet, like a wrong number or a missing update, can affect your construction budget, delay payments, or even lead to rework on site.
That’s why using construction project management software is a smarter, safer choice. It keeps everything in one place, helps your team stay aligned, and cuts down on manual tasks that often lead to mistakes.
Here’s how the right construction project management software helps save time and reduce costs:
Mastt is a great example of this. It’s a simple, easy-to-use tool made for project owners, client-side project managers, and consultants.
With Mastt, you get fast reporting, clear contract tracking, and smart payment tools, all without needing messy spreadsheets. You don’t have to chase numbers or fix broken formulas. It’s all accurate, visible, and ready when you need it.
10. Improve Job Site Safety to Avoid Fines and Injuries
Jobsite accidents can be expensive. One injury can lead to lost time, insurance claims, medical costs, and even legal fines.
Unsafe sites also lead to delays and low team morale. To reduce these risks, you need strong safety habits and regular checks across the site.
Good safety planning protects workers and, of course, your budget. When workers feel safe and know what to do, they work better, faster, and with fewer mistakes.
Here are smart ways to improve job site safety and reduce unnecessary costs and delays:
Let’s say a worker falls from an unprotected edge. Aside from the injury, you may face an OSHA fine, higher workers’ comp insurance, and project delays.
But if the right guardrails were installed and safety briefings were done, that incident could’ve been avoided. Safe sites help you save money, protect your team, and finish jobs without costly interruptions.
11. Maintain Your Equipment to Prevent Downtime Costs
Construction equipment is expensive to fix and even more costly when it breaks down mid-project. Every hour your machine is idle, you lose time, slow the job, and may need to rent a replacement. That’s why regular maintenance is key to reducing downtime and saving money.
Instead of waiting for something to break, follow a preventive maintenance plan. Small checks and tune-ups keep tools and machines running better for longer.
Here’s how to keep your equipment in top shape:
For example, skipping an oil change on a skid steer might seem small. But later, a failed engine could stop work for days and cost thousands. With simple routine checks, that kind of delay can be avoided.
12. Outsource Tasks That Cost You More In-House
Doing everything with your in-house team might seem cheaper at first, but it often leads to higher costs, delays, or poor results.
If a task takes too long, requires special skills, or slows your crew down, it may be better to outsource it. Smart outsourcing helps you reduce construction costs and get expert help without the overhead.
Here are tasks that often cost less when outsourced:
For example, if your team spends days fixing a machine or handling permit issues, you lose labor hours and delay progress. But outsourcing those tasks to people who do them daily saves you time, lowers risks, and keeps your team focused on building.
13. Motivate Workers to Be Efficient and Cost-Conscious
Your workers play a big role in your project’s budget. When crews are focused, engaged, and understand the impact of their work, they move faster, waste less, and take more care. Motivating your team doesn’t always need money. It needs communication, trust, and the right goals.
Here are simple ways to boost construction site efficiency and reduce construction costs:
Let’s say your team sees a shortcut to move materials faster or reduce waste during framing. If they’re encouraged to speak up, that small change could save hours or even days. When your crew feels trusted and included, they work better, stay longer, and help you cut costs without cutting corners.
14. Use a Construction Cost Reduction Checklist
Use this checklist to quickly spot where you can reduce construction costs across your project. Go through each item before, during, and after the job to ensure you’re not leaving money on the table.
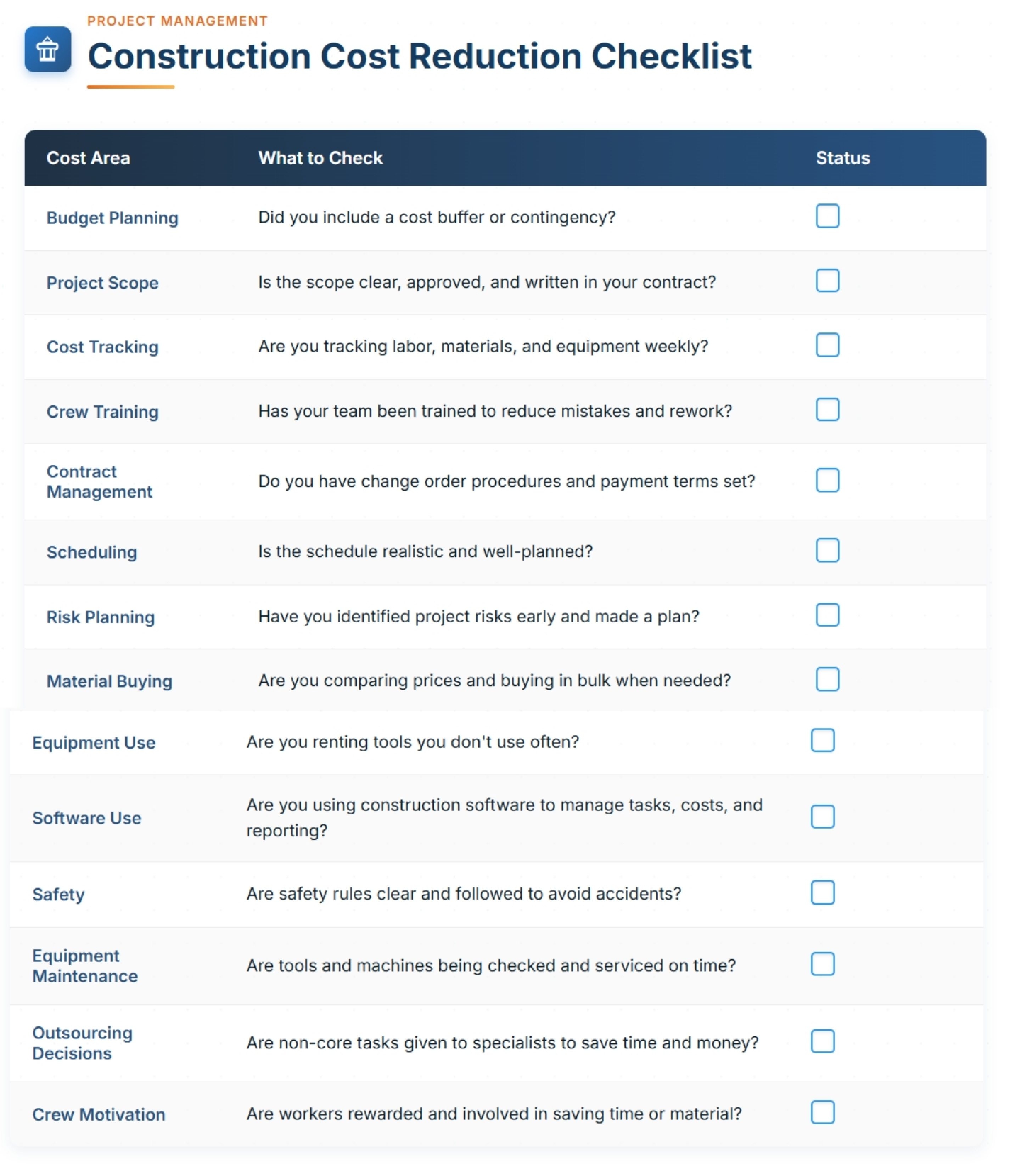
You can save this list or use it digitally at the start of every new project. It helps you stay in control, catch issues early, and keep every part of your build efficient and cost-effective. Even checking just a few of these boxes can lead to big savings over time.
Ready to Take Control of Your Construction Project Costs?
Sure, cutting costs in construction is about spending less. But it’s also about staying in control, like knowing where your money goes, catching problems early, and keeping your team on track. That’s exactly what Mastt helps you do.
Mastt is a construction project management software made for project owners, client-side project managers, and consultants. You can track costs, manage contracts, and send quick reports, all in one easy tool, without messy spreadsheets or delays.
If you want to save time, reduce mistakes, and stay on budget, Mastt helps you do it faster and smarter.