If you work in construction, you’ve likely come across the term Design and Construct (D&C) contract. It’s a common construction agreement where one contractor takes responsibility for both design and construction. This contract is widely used in medium to large projects, offering efficiency and cost certainty.
But is it the right choice for your project? This article breaks down how a D&C contract works, its advantages and risks, and when it makes the most sense to use one.
What is a Design and Construct Contract?
A Design and Construct contract is a legally binding agreement where one contractor is responsible for both designing and building a project. The client provides a project brief, and the contractor takes on the risk of developing the design, securing approvals, and delivering the completed construction.
D&C contracts are widely used in Australia, the UK, and other jurisdictions, especially for infrastructure and commercial projects. They shift design risk to the contractor, reducing client disputes over errors or changes. Contractors may use in-house designers or external consultants, but they remain fully accountable for the final outcome.
For a broader understanding of construction contract types, check out our guide on Construction Contracts.
Key Clauses to Consider in a D&C Contract
A Design and Construct (D&C) contract clearly defines the contractor’s responsibilities, helping to manage risks and ensure a smooth project delivery. Since the contractor handles both design and construction, the contract must set expectations for scope, liability, and how changes or disputes will be handled. Here are the key clauses that shape a strong D&C contract.
Scope of Works
This clause outlines everything the contractor is responsible for, from initial design to final construction. It should detail what is included in the contract, such as obtaining approvals, structural design, and compliance with building codes. A well-defined scope helps prevent misunderstandings and disputes over additional work or unexpected costs.
Design Liability & Warranties
Since the contractor is responsible for both the design and construction, they must ensure the design is sound and meets industry standards. This clause defines who is liable for design errors and how long the contractor remains responsible after project completion. It may also include warranties guaranteeing that the finished project meets performance and durability requirements.
Performance-Based Requirements
Instead of specifying exact materials like in a time and materials contract, many D&C contracts focus on performance outcomes. For example, rather than requiring a specific type of insulation, the contract may state that the building must meet a certain energy efficiency rating. This approach allows contractors flexibility in choosing solutions while ensuring the project meets functional and regulatory standards.
Variation & Change Orders
Changes to the design or scope are common in construction. This clause explains how changes are requested, reviewed, and approved. It sets rules for cost adjustments, time extensions, and who pays for modifications. Without a clear process, disputes over additional costs and delays can quickly arise.
Dispute Resolution Mechanisms
Even with a well-structured contract, disagreements can happen. This clause establishes how disputes will be resolved, whether through negotiation, mediation, arbitration, or court proceedings. Having a structured process in place prevents delays and expensive legal battles.
Pricing Mechanisms in Design and Construct Contracts
A Design and Construction contract can use different pricing structures depending on the project’s complexity, risk allocation, and payment preferences. These mechanisms determine how contractors are paid and how costs are managed. Choosing the right pricing method is crucial for balancing financial certainty and flexibility.
- Schedule of Rates or Bill of Quantities: Payments are based on pre-determined unit rates or time-based pricing. Contractors submit detailed breakdowns of completed work, and payments are made accordingly. This method is useful for projects where the scope may change, allowing adjustments based on actual work performed.
- Lump Sum Price: A fixed price is agreed upon before construction begins. The contractor assumes the risk of cost overruns but can benefit from cost efficiencies. This method provides cost certainty for the client but requires a well-defined scope to avoid disputes over additional work.
- Lump Sum with Schedule of Rates or Bill of Quantities: Its a lump sum payment that uses a schedule of rates to determine progressive payments. While the total contract price is fixed, payments are structured based on completed work. This approach ensures steady cash flow while allowing flexibility for certain cost elements.
- Staged Payments: Payments are released at key project milestones, such as design approval, structural completion, or final handover. This method helps manage cash flow for both the client and contractor, ensuring funds are available as the project progresses. It is commonly used in large-scale projects where measurable progress points justify payments.
- Cost-Plus Arrangements: Like in a cost plus contract, the client reimburses the contractor for actual costs plus an agreed profit margin. This method provides flexibility for projects with uncertain scopes but carries a higher risk of cost overruns. It is often used in complex projects where the design evolves during construction, making it difficult to fix costs upfront.
Standard Forms for Design and Construct Contracts
In Australia, Design and Construct (D&C) contracts are commonly structured using standard form agreements. These contracts provide a clear framework for managing responsibilities, risks, and project delivery expectations.
Several widely used standard form contracts define the obligations of both clients and contractors in D&C projects:
- AS 4300-1995: An early D&C contract covering project scope, risk allocation, and payment terms. Now largely replaced by AS 4902-2000.
- AS 4902-2000: The most widely used D&C contract in Australia. Defines contractor responsibilities, variations, time extensions, and dispute resolution.
- AS 4903-2000: Used for subcontracting in D&C projects, ensuring subcontractors work under similar terms as the main contract.
- PC-1 (1998): Developed by the Property Council of Australia. Common in commercial projects, offering more flexibility than AS contracts while maintaining structured risk management.
- GC21 (Government Contract 21): The preferred D&C contract for large government projects. Focuses on collaboration between the client and contractor, with mechanisms to manage risk, time extensions, and contract variations.
Design and Construct Example
The AS 4902-2000, published by Standards Australia, is a widely used Design and Construct (D&C) contract. It outlines key terms such as risk allocation, design responsibility, payment terms, and dispute resolution. Common in commercial and infrastructure projects, it provides a structured framework for contractor-led design and construction.
While AS 4902-2000 offers a solid foundation, many projects require modifications to fit specific needs. Clients and contractors often adjust design obligations, variation procedures, and risk provisions to align with project scope and financial goals.
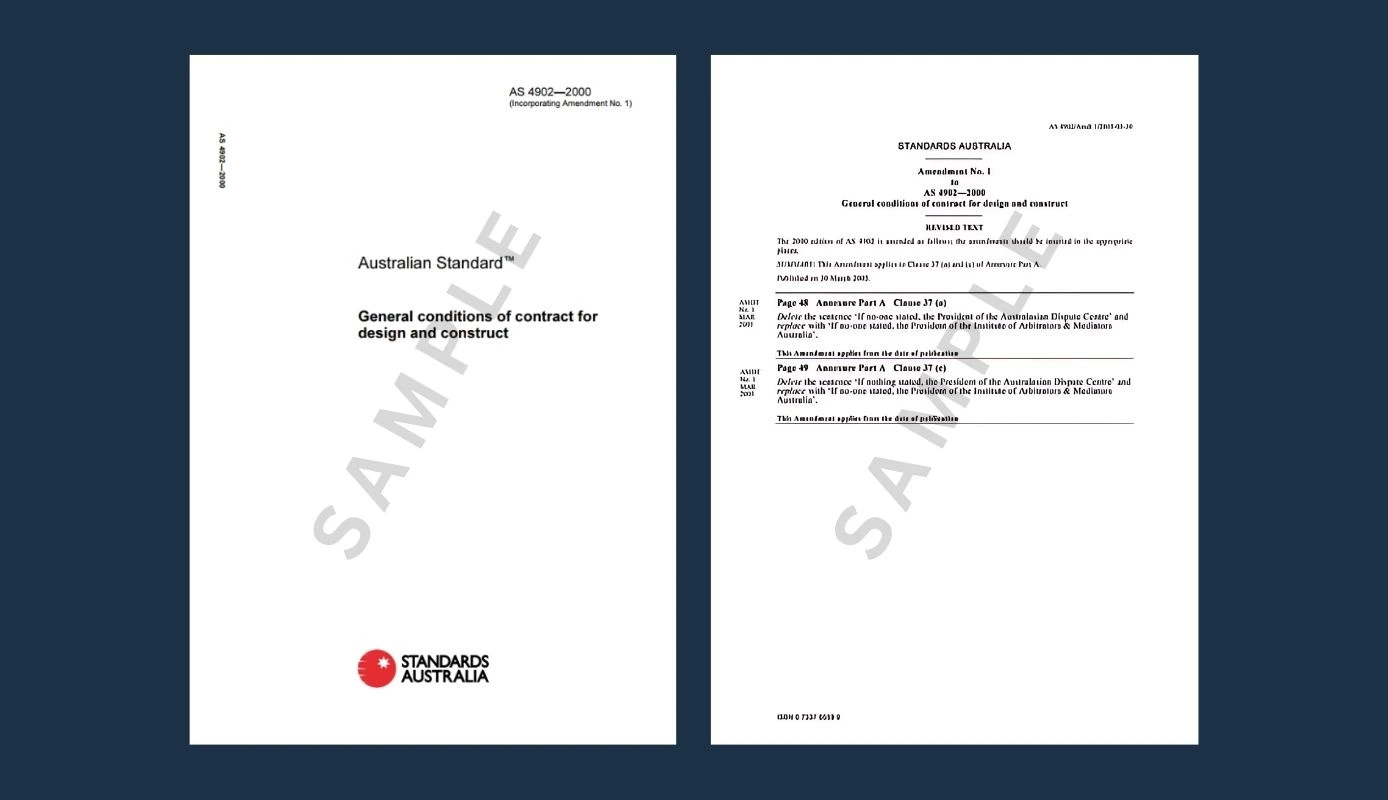
Advantages of a Design and Construct Contract
A Design and Construct (D&C) contract simplifies project delivery by placing both design and construction under one agreement. This structure benefits both clients and contractors, offering efficiency, cost control, and reduced risk. Here’s how:
For Clients:
- Single-Point Responsibility – One contractor handles everything, reducing coordination issues and potential disputes.
- Faster Project Delivery – Design and construction phases can overlap, shortening the overall timeline.
- Cost Certainty – Contractors price the project based on their design, minimizing unexpected cost increases.
For Contractors:
- Greater Control Over Design & Construction – More flexibility in choosing materials and construction methods.
- Reduced Risk of Design Errors – Since the contractor oversees the design, there’s less chance of conflicts over flaws.
- Competitive Advantage – Contractors can offer cost-effective solutions and innovations that improve project value.
A D&C contract can be an efficient and practical choice when speed, cost control, and clear responsibility are priorities. However, these benefits come with certain risks that both parties must carefully manage.
Disadvantages and Risks of a D&C Contract
While a Design and Construct (D&C) contract offers efficiency and cost control, it also comes with risks. Both clients and contractors must carefully manage these challenges to avoid disputes, delays, and unexpected costs.
For Clients:
- Less Design Control – Once the contract is awarded, clients have limited influence over design details. Changes can be expensive and may lead to delays.
- Potential for Cost-Cutting – Contractors may prioritize cost savings over quality, using cheaper materials or alternative construction methods to stay within budget.
- Reliance on Contractor’s Expertise – The success of the project depends on the contractor’s ability to deliver both a functional design and high-quality construction. Poor execution can lead to costly problems.
For Contractors:
- Higher Risk Exposure – Since the contractor is responsible for both design and construction, they bear the risk of design errors, compliance issues, and construction defects.
- Tight Budgets & Margins – Pricing the project accurately is critical. Underestimating costs can lead to financial losses, while overpricing may make bids less competitive.
- Complex Coordination – Managing both design and construction teams requires strong planning and communication. Poor coordination can cause rework, delays, and disputes.
A D&C contract can be an effective model, but both parties need to understand and mitigate these risks to ensure a successful project.
When to Use a Design and Construct Contract?
A Design and Construct (D&C) contract works best when efficiency, cost certainty, and streamlined project management are priorities. It is commonly used in large-scale projects where the client wants a single point of responsibility for both design and construction. However, this contract type is not always the right choice, especially for projects requiring high levels of design flexibility.
Best Suited For:
- Large Infrastructure Projects: Roads, bridges, and airports benefit from a contractor-led approach that speeds up delivery and reduces coordination issues.
- Commercial Developments: Office buildings, shopping centers, and industrial facilities where standard designs can be adapted quickly.
- Projects with Repeatable Designs: Chain retail stores, hotels, and franchise buildings where a consistent design is used across multiple locations.
Not Ideal When:
- Client Requires Full Design Control: If the client wants to be deeply involved in design decisions, a traditional contract may be a better option.
- Highly Bespoke or Evolving Designs: Unique, complex projects like high-end architecture or experimental builds often need flexibility that a D&C contract does not provide.
Final Notes on Design and Construct Contract
A Design and Construct (D&C) contract is a legal framework that defines responsibilities, risk allocation, and financial arrangements between clients and contractors. Understanding its structure, key clauses, and pricing mechanisms is essential for ensuring a fair and effective agreement.
Whether used for infrastructure, commercial developments, or large-scale projects, a well-structured D&C contract provides clarity and efficiency, but only when its risks and limitations are carefully managed.