Managing payments for materials off-site is crucial for construction project management. It involves understanding how these payments fit into the progress claim process and integrating them effectively into project workflows.
We'll explore best practices and challenges, ensuring you're equipped to handle these agreements with confidence. This includes key considerations that are essential for managing payments efficiently and clearly.
What are Materials Off-Site Payments?
Materials off-site payments are an arrangement where contractors are compensated for materials stored off the construction site but earmarked for the project. This system can be beneficial for contractors managing large or high-value materials.
Before we dive into the specifics, let's explore the core elements that define materials off-site payments and how they work within construction contracts.
What Does "Materials Off-Site" Mean?
Materials off-site refers to items purchased, stored, and prepared for a construction project but not yet delivered to the site. Examples include:
- Custom-fabricated components awaiting shipment.
- High-value materials like steel beams stored in secure warehouses.
- Specialty items sourced internationally and held at port facilities.
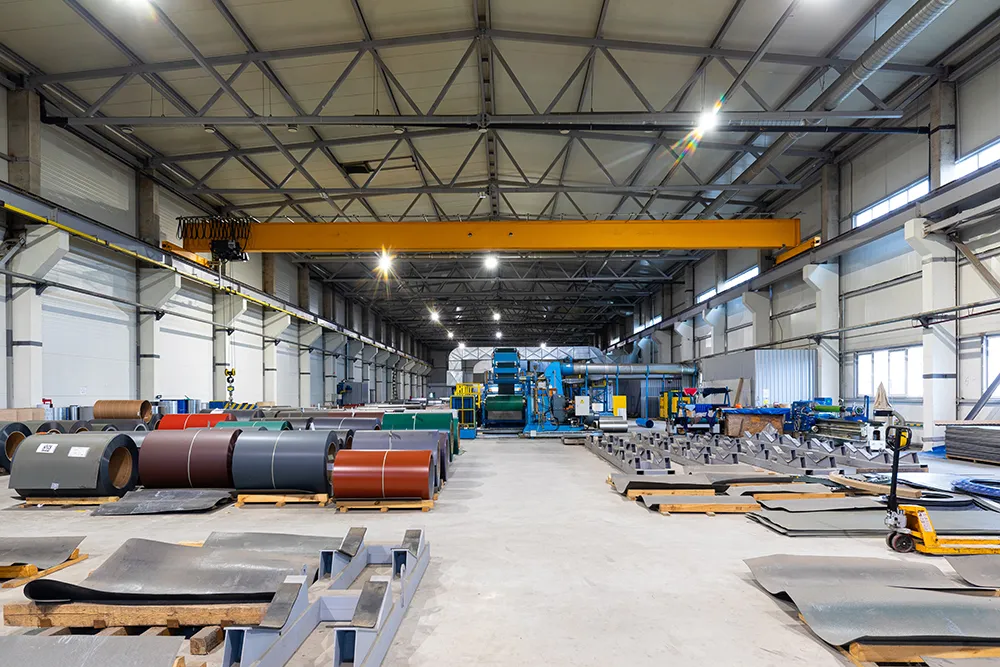
These materials are often certified for payment once their ownership and intended use are verified.
Types of Construction Materials Stored Off-Site
Construction projects often involve the storage of various materials off-site, which can include:
- Building Materials: Items such as lumber, steel, and concrete are fundamental to the structural integrity of any construction project. These materials are often stored off-site to ensure they are protected from environmental damage and theft.
- Finishing Materials: This category includes flooring, roofing, drywall, and other materials used to complete the interior and exterior of a building. Storing these off-site helps in managing space constraints on the project site.
- Mechanical and Electrical Materials: HVAC systems, plumbing fixtures, and electrical components are critical for the functionality of a building. These materials are often stored off-site to ensure they are kept in optimal conditions until needed.
- Specialized Materials: Items such as glazing, insulation, and fireproofing materials are stored off-site to maintain their quality and readiness for specific trades.
- Site Materials: Scaffolding, formwork, and other equipment used to support the construction process are often stored off-site due to their bulk and the need for secure storage.
- Plant and Equipment: Heavy machinery like cranes and excavators are stored off-site to prevent damage and ensure they are available when required.
- Project Materials: Specific components such as roofing, siding, and windows are stored off-site to ensure they are protected and ready for installation.
- Other Materials: Landscaping, paving, and other site work materials are stored off-site to manage space and protect them from the elements.
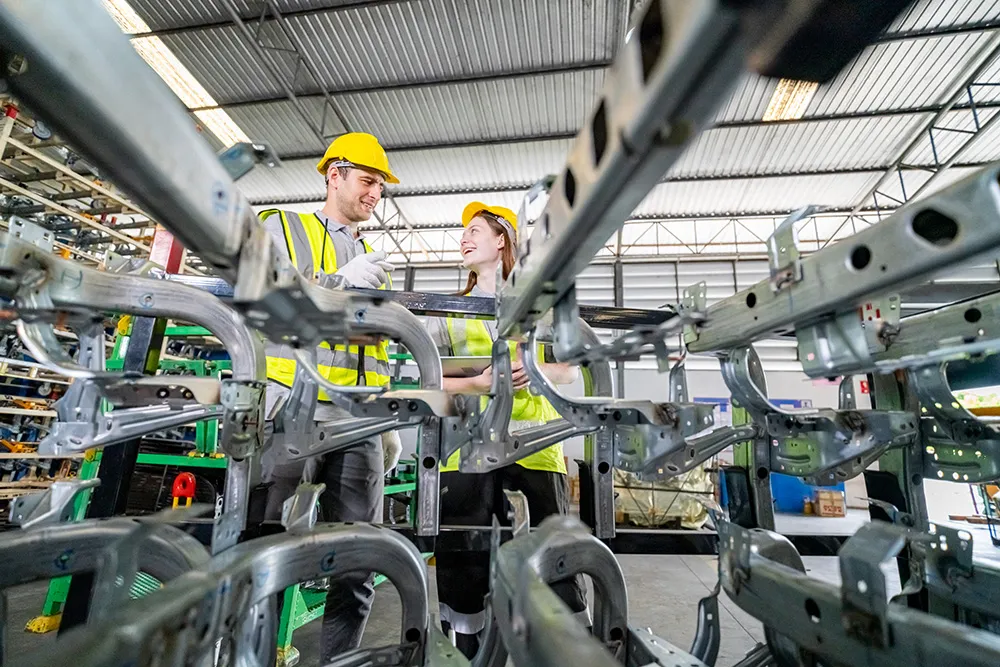
These materials are often stored off-site due to limited space on the project site and to ensure they are protected from the elements and potential damage. The storage of these materials off-site requires careful planning and management to ensure they are delivered to the project site in a timely and efficient manner.
In addition to the types of materials stored off-site, it’s also important to consider the following:
- Early Ordering: Ordering materials early can help ensure they are available when needed, but it also increases the risk of damage or loss during storage. Proper planning and secure storage solutions are essential.
- Insolvent Contractor: If a contractor becomes insolvent, the ownership of materials stored off-site may be at risk. Clear payment terms and contract documents are crucial to protect all parties involved.
- Payment Terms: Payment terms should be clearly defined in the contract to ensure the contractor is compensated for materials stored off-site, avoiding disputes over payment.
- Supplier Insolvency: If a supplier becomes insolvent, the delivery of materials stored off-site may be jeopardized. Selecting reliable suppliers and having contingency plans in place is vital.
- Site Storage: Materials stored on-site should be properly secured and protected from the elements to prevent damage or loss.
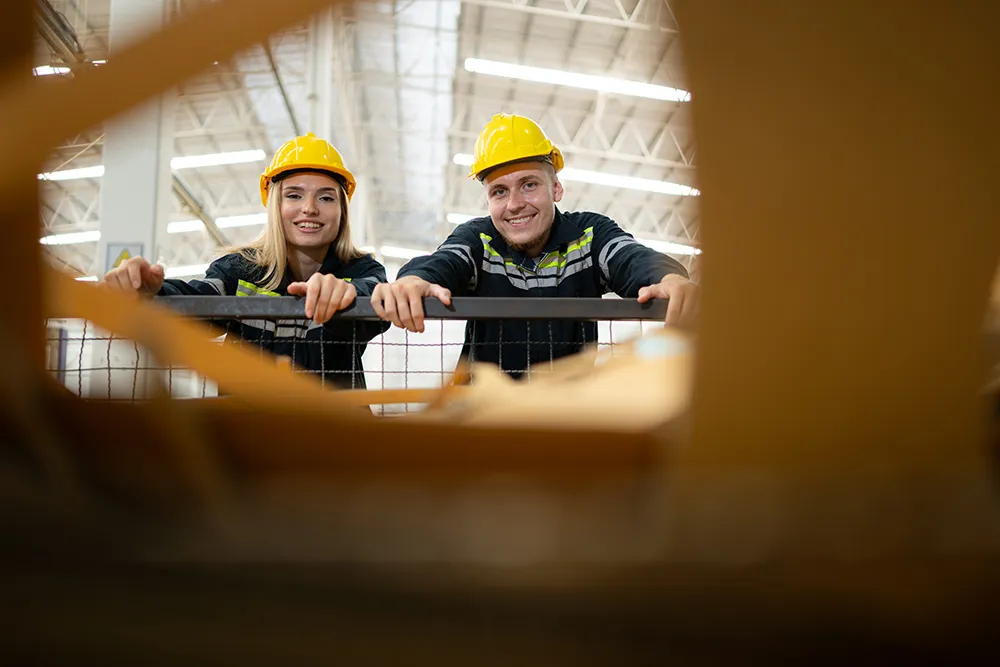
By understanding the types of construction materials stored off-site and the associated risks and considerations, project managers and contractors can better plan and manage the storage and delivery of these materials to ensure successful project outcomes.
Key Steps in Certifying Advance Payment for Materials Off-Site
To ensure smooth processing of payments for materials off-site, follow these essential steps:
- Ownership Documentation: Ensure materials are clearly owned by the project employer through invoices or receipts. The contract price reflects the total costs associated with the project, including overheads and profit, and impacts the certification of materials off-site.
- Storage Certification: Verify that materials are stored in a secure, insured location.
- Inspection and Certification: Conduct third-party inspections to confirm the materials’ readiness for the project.
- Incorporation in Progress Claims: Include certified off-site materials in your regular progress claim submissions.
.webp)
For a detailed guide on submitting effective progress claim software, refer to this resource.
Why Payment for Materials Off-Site Matters
The practice of paying for materials off-site addresses several pain points in construction. It impacts project cash flow, supply chain efficiency, and contractor relationships. Understanding its significance is essential for both employers and contractors.
Impact on Cash Flow and Project Financing
Paying for off-site materials allows contractors to:
- Maintain healthy cash flow during the procurement phase.
- Secure bulk orders or custom items without immediate financial strain.
- Avoid delays caused by payment disputes or funding gaps.
Proper planning also aligns with broader construction cashflow strategies, ensuring financial stability throughout the project lifecycle.
Risk Mitigation Through Insurance and Contracts Against Supplier Insolvency
Clear terms in the construction contract reduce risks. For example:
- Insurance Policies: Protect materials from theft or damage during storage.
- Vesting Certificates: Secure employer ownership before materials leave the vendor’s location.
These measures align with broader concepts like cash retention vs bank guarantee to ensure smooth financial operations.
Challenges & Considerations in Off-Site Payments
Materials off-site arrangements come with challenges that require strategic planning. Address these proactively to ensure a seamless process.
Practical Risks to Manage
Some risks include:
- Storage Issues: Poor conditions or lack of security can lead to material damage.
- Ownership Disputes: Unclear transfer of title could result in legal conflicts.
- Project Delays: Mismanagement in logistics or approvals could delay material delivery.
Pragmatic Approaches to Risk Management
Mitigate risks with these strategies:
- Use detailed contracts outlining material specifications, storage requirements, and ownership clauses.
- Conduct regular audits and inspections of storage facilities.
- Maintain communication with vendors and insurers to ensure alignment.
Best Practices for Materials Off-Site Payments
Both employers and contractors can benefit from following these best practices:
- Establish Clear Contract Terms: Define payment milestones, ownership transfers, and inspection protocols.
- Incorporate Flexible Payment Schedules: Account for unforeseen delays or changes in material readiness.
- Utilize Digital Tools: Track and document material movements using construction payment software.
Aligning these practices with effective progress payment strategies ensures smoother financial operations and fewer disputes.
From Contract Clauses to Construction Success
Materials off-site payments are more than a contractual nuance. They’re a practical tool for managing costs, timelines, and relationships in construction projects.
By embracing these practices, you’ll not only mitigate risks but also foster trust and efficiency within your project teams. Explore additional considerations, such as the nuances of a final claim in construction, to comprehensively manage project finances and expectations.