Successful construction projects don't just happen by chance. They require careful planning and smart decision-making about how work gets executed. So, what really drives this success? The answer lies in mastering means and methods of construction.
Definition of Means and Methods of Construction
Means and methods in construction defines the resources used to build a project and the processes for using those resources effectively. This fundamental concept drives every construction decision, directly impacting project safety, quality, and productivity.
The term “means” and “methods” breaks into two essential parts:
- "Means" represents all physical resources - the equipment, materials, labor, and tools needed for construction.
- "Methods" covers all technical procedures - the work sequences, safety protocols, and coordination strategies that guide how those resources are used.
Think of means as the "what" and methods as the "how" in construction execution. Every successful project requires both elements to work together effectively.
Let's have some examples and examine how means and methods work together in construction and see their difference:
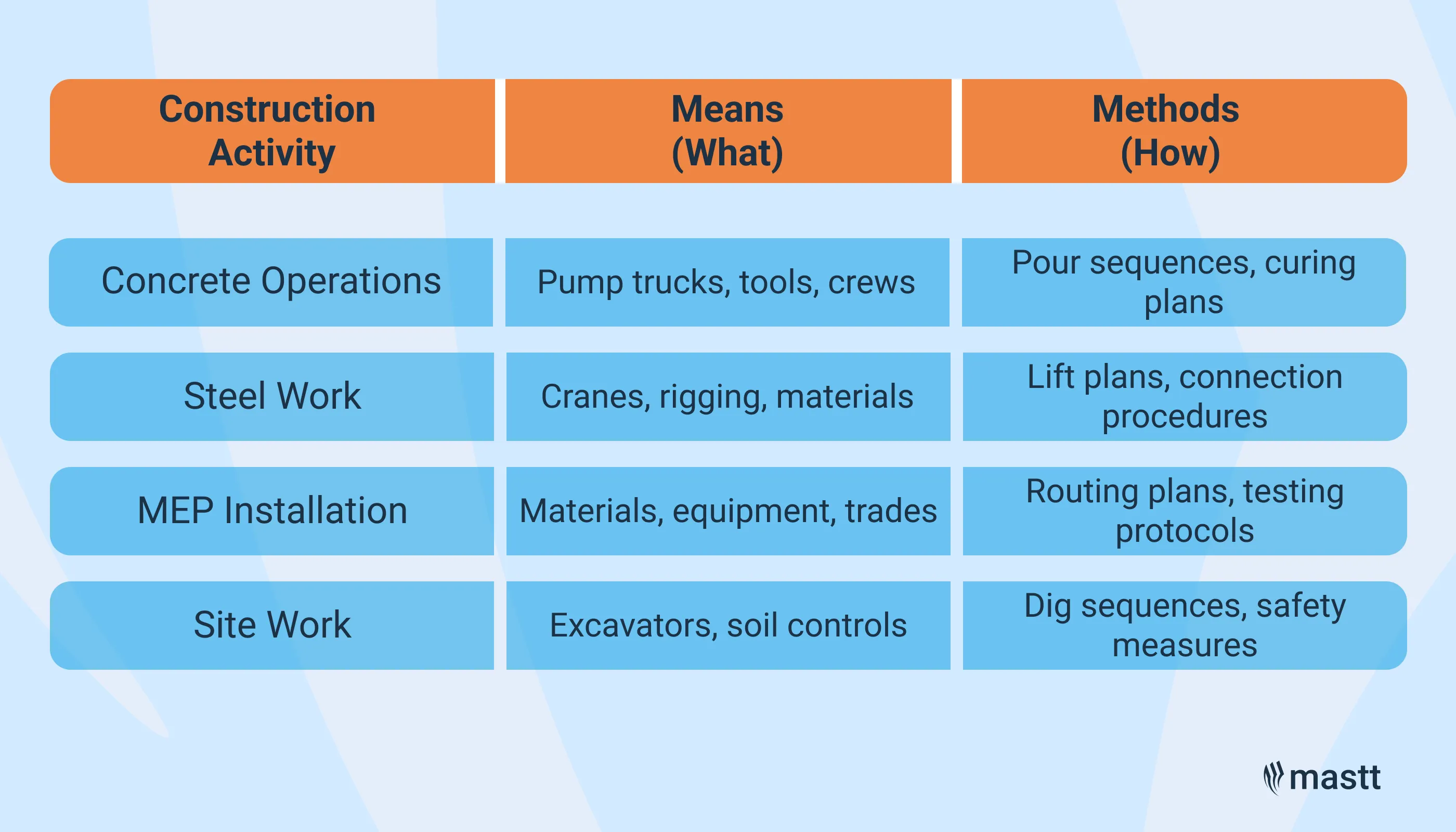
Why does understanding this relationship matter so much? Because every construction activity depends on choosing the right resources and using them effectively. Your concrete crews need both proper equipment and clear procedures to achieve quality results.
Who is Responsible for Construction Means and Methods?
General contractors hold primary responsibility for means and methods decisions on construction projects. They use their direct field experience to determine how work gets executed safely and efficiently while maintaining quality standards.
However, construction teams operate within a structured system of responsibilities where each party contributes specialized expertise. Let's examine how these key project parties work together:
- General Contractors: Lead all means and methods decisions, develop work plans, coordinate trades, manage safety programs, and control daily operations based on direct construction experience.
- Engineers: Provide technical validation for procedures affecting structural integrity, review temporary support designs, verify complex installation methods, and help solve engineering challenges during construction.
- Architects: Ensure construction methods maintain design intent, verify building envelope integrity, review finish installation procedures, and validate that work meets aesthetic requirements.
- Project Owners: Monitor overall progress, verify safety compliance, track quality standards, manage budget performance, and ensure regulatory requirements are met while respecting contractor authority over means and methods.
- Trade Contractors: Contribute specialized expertise about their work requirements, coordinate with other trades, and implement specific installation procedures within their scope.
Regular coordination between these parties ensures successful project delivery through:
When challenges arise, each party contributes their expertise while maintaining clear lines of authority. This structured approach keeps projects moving forward efficiently while meeting all technical, safety, and quality requirements.
How Do Means and Methods Impact Project Success?
Construction means and methods affect project success by influencing safety, quality, productivity, and overall outcomes. To explore these impacts further, see the following sections for detailed insights.
Direct Effects on Safety and Quality
Safety starts with proper planning, and your means and methods are the foundation. To avoid incidents, you must build safety controls into your procedures before work begins. Let’s break this down:
- Access Planning: Ensure workers and equipment have clear, safe pathways to move around.
- Fall Protection: Install systems before anyone works at heights to avoid accidents.
- Equipment Operations: Define clear zones and set up communication protocols for safe usage.
- Emergency Response: Always have quick access to medical or fire services.
- Training: Make sure your crew knows the procedures to work safely.
When it comes to quality, sticking to planned means and methods of construction is just as crucial. Clear procedures, inspections, and documentation ensure the work meets standards and prevents costly mistakes from recurring.
Cost and Schedule Implications
Your decisions around means and methods don’t just affect quality—they hit your budget and timeline, too. Smart planning can keep costs down and schedules on track. Here’s what to focus on:
Efficient planning ensures you’re working at a realistic pace while keeping resources available and managing weather disruptions effectively.
Risk Management Through Proper Planning
From my experience, no project is without risks, but good planning helps me keep them under control. Here’s what I believe are high-risk tasks that need extra attention:
- Structural Stability: Use monitoring systems to catch potential movement early.
- Underground Work: Protect utilities and manage soil stability.
- Critical Lifts: Develop detailed plans for hoisting heavy materials.
- Confined Spaces: Follow strict entry rules and monitor air quality.
- Weather Protection: Put systems in place to shield work from environmental damage.
Understanding common construction sign meanings is also essential for maintaining safe work environments. Signs like “Caution: Hard Hat Area” or “Restricted Access” provide clear guidance to workers and visitors, preventing potential hazards.
By addressing these risks head-on, you can keep your project moving smoothly without unexpected setbacks.
Environmental and Community Impact Considerations
Your project doesn’t happen in isolation—it impacts the environment and the community around it. So, how do you ensure your operations stay responsible?
Planning ahead not only protects the environment but also builds trust and goodwill with the community, ensuring smoother project execution.
Planning and Developing Construction Means and Methods
Planning construction means and methods is critical for delivering successful projects. As a project manager, every choice you make can influence your timelines, budgets, and the overall safety of your team. Let’s break this down and ensure your plans are effective and actionable.
Site Analysis and Logistics Planning
Let’s start with your site. The layout and conditions of your site define how your project will flow.
Take a moment to think: Where’s the best spot for your equipment to maximize efficiency? How can materials move without creating unnecessary bottlenecks? And what potential obstacles could slow down your team?
Here’s what to prioritize:
- Site Access: Plan clear and efficient routes for deliveries and equipment.
- Storage Areas: Choose protected locations for essential materials.
- Vertical Transportation: Place cranes and lifts where they enhance productivity.
- Trade Workspace: Assign ample room for your crews to work without interruption.
- Safety Zones: Design safe pathways to protect your workers.
These decisions form the backbone of your site utilization plan. For example, staging areas should enhance material flow, while smart equipment placement prevents disruptions during peak operations.
Resource Allocation Strategies
Getting the right resources to the right place at the right time is essential. Matching labor, equipment, and materials with project requirements is your key to avoiding delays and staying productive.
As you monitor progress, make adjustments as needed. If production slows, check if your crew size needs tweaking or if equipment is being underutilized. These small changes can have a big impact on overall efficiency.
Equipment and Tool Selection Criteria
The construction tools you pick aren’t just for the job—they’re for getting the job done safely and efficiently. Every piece of equipment must fit your project’s needs and site conditions.
When choosing equipment, ask yourself:
- Production Capacity: Can it handle the workload without overspending?
- Site Accessibility: Will it fit within the space and terrain constraints?
- Support Needs: Are power, fuel, and maintenance requirements manageable?
- Safety Features: Does it include proper protections for operators?
- Backup Options: Do you have alternatives ready for potential breakdowns?
For instance, if your crane’s capacity limits steel assembly, you may need to adjust your rigging plans. Similarly, concrete pump reach constraints might call for a revised pouring strategy to avoid unnecessary delays.
Technology Integration in Construction Methods
The right technology can simplify even the most complex tasks, ensuring your means and methods of construction are as accurate and efficient as possible.
Imagine using 3D models to pre-plan installations or relying on GPS for layout accuracy. These tools don’t just help you avoid mistakes—they let your teams work smarter and faster, saving you time and resources.
When you prioritize site analysis, resource allocation, equipment selection, and technology, your construction means and methods become actionable and efficient.
Quality Control in Construction Methods
Quality control in construction methods is critical to delivering successful projects. Ensuring quality begins with proper means and methods planning.
As a project manager, your job is to implement systems that identify and prevent potential problems before they escalate. Let’s explore how effective quality control can keep your project on track.
Establishing Quality Standards
Establishing clear quality standards is the foundation of successful construction quality control. These standards must align with project specifications and industry requirements. Your field teams need step-by-step procedures to understand exactly what’s required.
Focus on these key areas of quality control in construction methods:
- Installation Procedures: Clear, step-by-step guidelines for executing critical tasks.
- Material Handling: Proper storage and protection requirements.
- Testing Protocols: Verified methods to ensure performance and reliability.
- Documentation Systems: Records that demonstrate compliance with standards.
- Non-Conformance Control: Procedures for identifying and resolving quality issues.
Inspection and Testing Procedures
Inspections are a core element of quality control in construction methods. They verify that work complies with project standards at critical milestones. Here’s how inspections should be structured:
These inspection checkpoints help you catch and address problems early, reducing the likelihood of costly rework. Documentation of these results provides a clear trail of compliance and highlights any recurring issues.
Documentation Requirements
Comprehensive documentation is essential for proving that work meets quality standards. Quality records must capture every inspection, test, and corrective action to protect your project and ensure continuous improvement.
Here’s what to document:
- Inspection Reports: Daily records of work compared to project standards.
- Test Results: Verified performance data from required testing procedures.
- Material Certifications: Proof of compliance with material specifications.
- Non-conformance Reports: Details of issues and their resolutions.
- Photo Documentation: Visual evidence of completed work.
Organizing these records ensures transparency and simplifies audits or claims processes when necessary.
Corrective Action Protocols
No project is immune to quality issues, and we all know that. A well-defined corrective action process ensures that problems are resolved efficiently and effectively.
Follow these steps for handling non-conformance:
- Identify the Issue: Document exactly what is wrong.
- Analyze the Root Cause: Investigate why the problem occurred.
- Plan a Solution: Develop detailed steps to correct the issue.
- Implement the Fix: Ensure repairs or replacements are carried out properly.
- Verify the Solution: Confirm that corrective actions meet project standards.
Project managers play a critical role here, coordinating with the construction superintendent to ensure solutions are practical and cost-effective. Quality managers verify compliance while you track the overall impact on timelines and budgets.
How Do Changes Affect Means and Methods?
Changes in a construction project require flexibility in means and methods. As a project manager, you’ve likely dealt with these challenges—unexpected site conditions, design updates, weather disruptions, or resource constraints. Let’s discuss how to adapt effectively while keeping safety, quality, and efficiency intact.
Adapting to Site Conditions
Unexpected site conditions, like buried utilities or unforeseen obstacles, demand immediate adjustments. In these cases, you’ll need to:
- Modify Sequences: Protect existing utilities without slowing progress.
- Update Access Routes: Create safe, efficient pathways around obstacles.
- Revise Staging Plans: Optimise layouts to fit new site realities.
Keeping a close eye on your site through regular monitoring ensures you catch and address these surprises early.
Managing Design Changes
Design changes happen, whether they involve shifting load paths or updating MEP requirements. When they do, make sure to focus on:
- Revising Coordination Plans: Share updated designs promptly with your teams.
- Adjusting Schedules: Ensure procurement and installation plans align with the new requirements.
Clear communication is key here. Keeping your crew informed helps them execute efficiently, even with new parameters.
Handling Weather and Resource Challenges
You can’t control the weather, but you can prepare for it. Extreme temperatures, high winds, or material delays require flexible strategies:
- Plan for Contingencies: Use backup equipment or alternative suppliers to stay on schedule.
- Train for Flexibility: Equip your teams to adapt to labor shortages or schedule changes.
Monitoring forecasts and supply chains helps you anticipate and mitigate these challenges before they escalate.
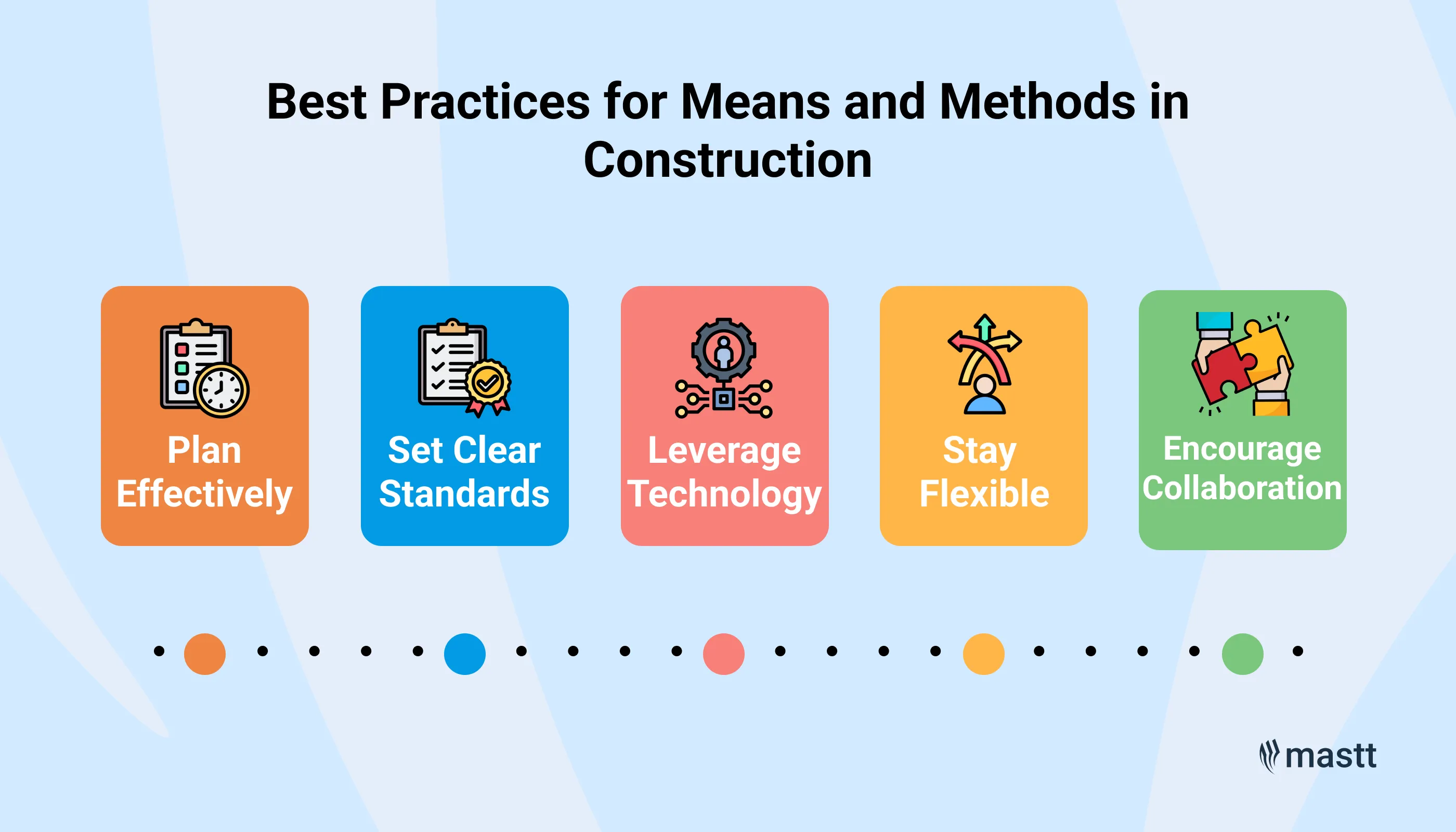
Best Practices for Means and Methods in Construction
To master means and methods of construction, you need strategies that prioritize safety, quality, and efficiency. Let’s break down what project managers like you can do:
- Plan Effectively: Start by thoroughly analyzing your site and project requirements. Use tools like Mastt to simplify workflows, reduce delays, and avoid bottlenecks. Mastt’s planning features help keep your team aligned with project goals.
- Set Clear Standards: Provide your team with detailed, actionable procedures, including step-by-step protocols and quality benchmarks. Mastt can centralize these documents, making them easily accessible to your entire team.
- Leverage Technology: Modern construction thrives on innovation. Construction project management tools like Mastt allows for seamless integration with reporting systems, improving visibility and accountability across your operations.
- Stay Flexible: Projects are dynamic, with unexpected conditions or design updates requiring quick adjustments. Mastt’s real-time reporting and monitoring features ensure you can adapt without delays.
- Encourage Collaboration: Foster strong communication among field teams, contractors, and engineers. Mastt’s collaboration features make it easier to coordinate and share updates in real time, keeping everyone aligned.
By applying these best practices and leveraging Mastt’s capabilities, you’ll build efficient, adaptable means and methods, ensuring the success of your construction projects.