Managing a construction project or a large-scale capital project is no small feat. As anyone in the industry knows, it’s more than just pouring concrete or erecting steel frames. Behind the scenes, there's a critical framework that keeps things moving—supply chain project management. This method of managing workflows, materials, and resources has become a game-changer for modern construction. It ensures that every nut and bolt arrive on time, every process flows smoothly, and budgets are kept intact.
Speaking of effective management, it’s worth exploring Construction Project Management as the backbone for handling the many moving parts in construction. When supply chain project management works hand-in-hand with construction strategies, projects not only come in on time but with fewer headaches and unexpected costs.
What Is Supply Chain Project Management?
At its core, supply chain project management integrates the processes that connect material procurement, logistics, contractors, and timelines into one seamless flow. Think of it as the backstage crew at a big show—coordinating each element so everything appears flawless on stage. Without this type of project management in the supply chain, your construction efforts could quickly descend into chaos, with late deliveries, cost overruns, and frustrated stakeholders.
Let’s break it down:
- Materials: From steel beams to HVAC units, materials must be ordered, tracked, and delivered at the right time. Too early, and you’re stuck paying for storage. Too late, and your project is delayed.
- Logistics: Trucking, shipping, and on-site handling need tight coordination to prevent bottlenecks.
- Contractors and Suppliers: Multiple teams are involved, and without clear communication, things can spiral out of control.
This is where an introduction to supply chain management becomes essential—knowing how to plan, manage, and monitor every moving piece from start to finish ensures smooth operations and avoids painful project delays.
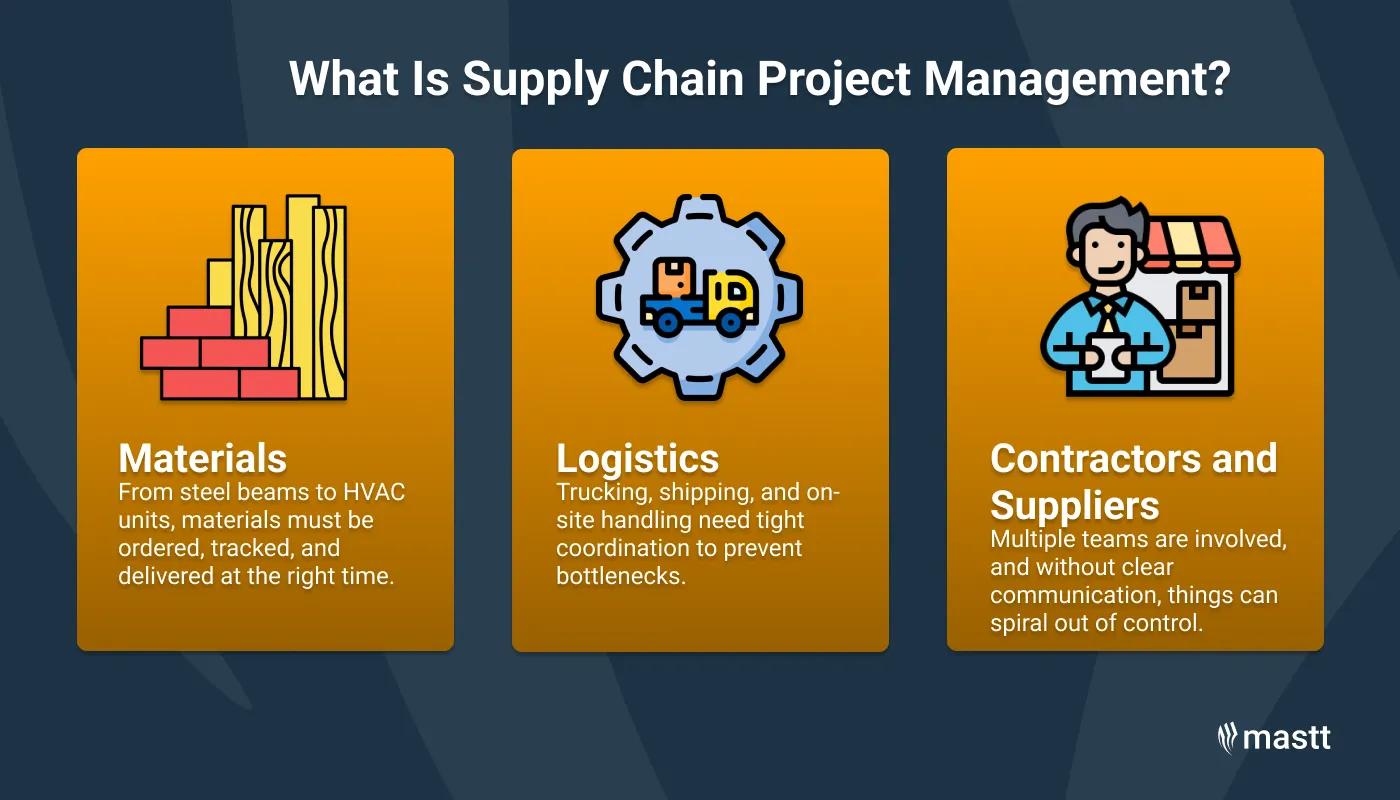
Why Supply Chain Project Management Is Critical in Construction
Let’s face it: in the construction industry, things rarely go exactly as planned. Materials don’t always arrive on time, weather doesn’t always cooperate, and subcontractors sometimes have their own priorities. Supply chain project management steps in to help anticipate these issues before they happen, using data and collaboration tools to create contingency plans.
Avoiding Project Delays
Picture this: A construction company is building a new office complex. The supplier of custom glass windows promises delivery in eight weeks. But, without a strong project management strategy in the supply chain, no one follows up, and the windows arrive two months late. Suddenly, everything from interior work to final inspections is thrown off.
Now imagine if supply chain project management had been in place. Automated reminders would have prompted a follow-up with the supplier weeks earlier. Contingency options—such as alternative glass providers—would have already been identified, minimizing any impact on the project schedule. To dive deeper into this aspect, explore the importance of construction quality control for mitigating risks like these.
The Benefits of Effective Supply Chain Project Management for Capital Projects
Capital projects—think airports, highways, or energy facilities—are often even more complex than your standard construction project. These projects typically require:
- Multiple suppliers across different regions or countries
- Longer timelines with extensive planning phases
- High-stakes budgets where overruns can mean millions in additional costs
A solid project management approach in supply chain ensures that all these complexities are well-managed. How? By creating a real-time flow of information between all involved parties, from contractors to suppliers and everyone in between.
Additionally, a reliable system allows companies to track every stage of the process—from sourcing materials to on-site installation—ensuring everything aligns with project milestones. This can be the difference between meeting your deadlines or facing significant delays that affect public openings and investor trust. If you're unsure how to create a detailed project overview, consider using a project charter template to ensure alignment across all parties from day one.
Pro Tips: How to Improve Supply Chain Management in Construction
Want to stay ahead of common supply chain issues? Here are some practical tips that can make a real difference:
- Build strong relationships with suppliers – Your vendors are partners. Open communication can help solve problems quickly.
- Use technology to your advantage – Project management software can track shipments, timelines, and budgets in real time.
- Plan for contingencies – Weather delays or supplier hiccups will happen. Have a Plan B ready.
- Collaborate with all stakeholders early – Involving subcontractors and suppliers from the start helps prevent miscommunication down the line.
If you’re managing complex portfolios with multiple projects running simultaneously, check out our guide on how to manage a project portfolio for more insights.
Supply Chain Management as a Key to Project Success
Whether you’re managing a small-scale construction project or overseeing a massive capital initiative, supply chain project management is a crucial piece of the puzzle. It’s not just about moving materials from A to B—it’s about anticipating potential issues, creating efficient workflows, and aligning everyone involved toward a common goal.
When done right, it reduces costs, speeds up timelines, and eliminates many of the “surprises” that can derail a project. At the end of the day, the success of your construction project may come down to how well you manage the unseen logistics and workflows that keep everything moving. And that’s the magic of supply chain project management—working behind the scenes to keep the show on the road.