In project management, variance analysis is a method used to compare planned costs, timelines, and resources against actual performance to spot deviations early and prevent financial headaches.
For project managers, owners, and stakeholders, variance analysis is an essential tool to detect early warning signs and prevent cost overruns or delays before they impact the project. But how do you systematically analyze variances, quantify their impact, and take corrective action?
Let’s break it down step by step—starting with what variance analysis means in construction and how real-time data and digital tools like Mastt can enhance accuracy and decision-making.
What Is Variance in Project Management?
Simply put, a variance is the difference between what was planned and what actually happens. In construction project management, this applies to costs, schedules, and even labor or materials. Some variances are minor, while others can throw the whole project off balance.
The most common types of project variances are:
- Cost Variance (CV): Are we spending more or less than expected?
- Schedule Variance (SV): Is the project ahead of schedule, or are we falling behind?
- Resource Variance: Are labor, materials, or equipment usage in line with projections?
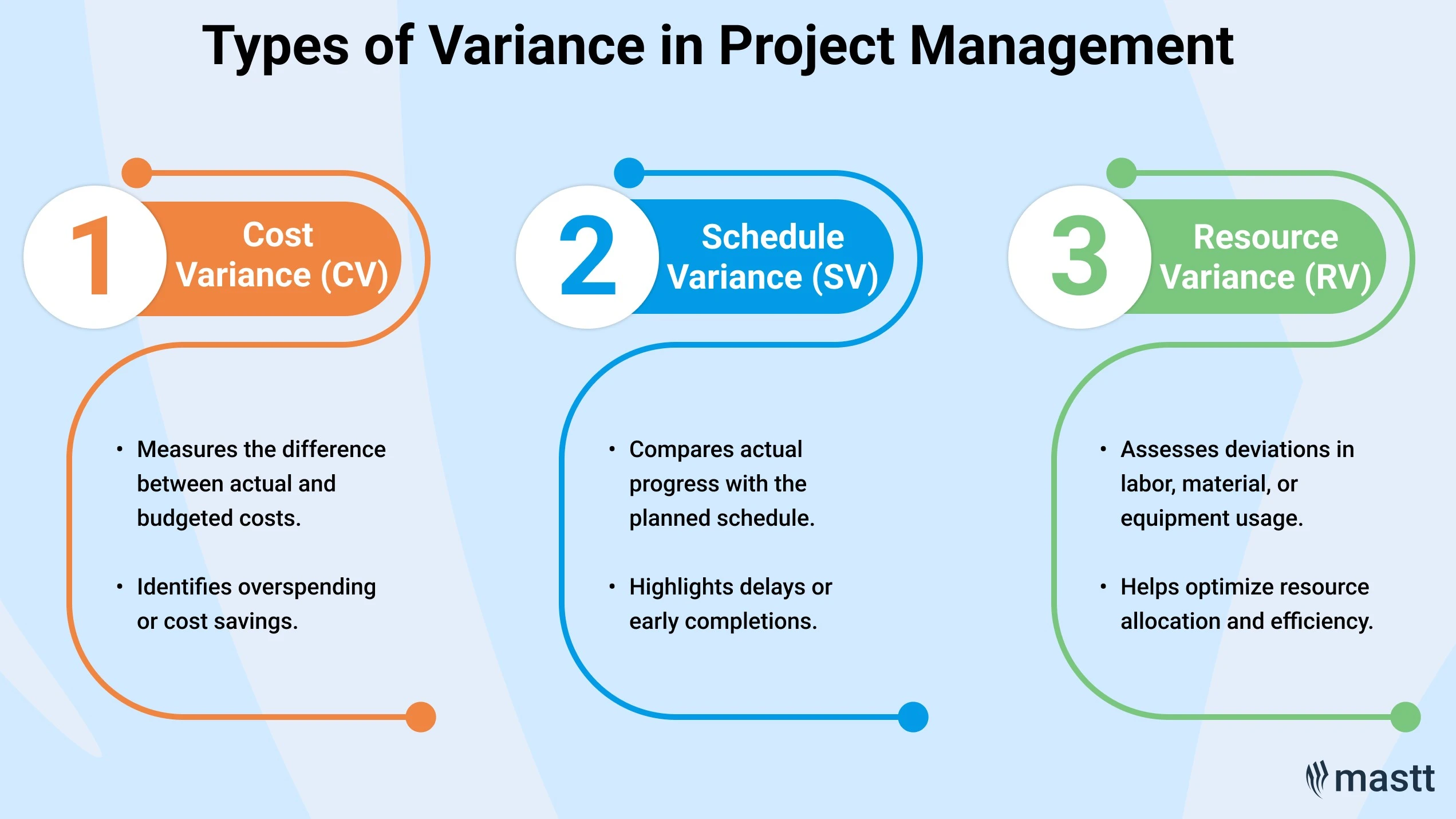
Let’s say a construction project was budgeted at $5 million, but expenses hit $5.5 million. That extra $500,000 is a cost variance—and if left unchecked, it could eat into profits or push the project into financial trouble.
Mastt simplifies this process by providing real-time cost tracking, automated variance reporting, and forecasting tools—all in one platform. This allows project teams to detect financial discrepancies instantly without relying on outdated spreadsheets.
Why Does Variance Analysis Matter?
Project managers, owners, and everyone involved doesn't like surprises—especially when they cost money. Variance analysis keeps financial surprises to a minimum by showing where the budget is leaking, where delays are forming, and what actions must be taken.
Here’s why variance analysis is a must-have in project cost management:
- Keeps the Budget in Check: Tracks where money is going and helps adjust spending before overruns become a problem.
- Improves Forecasting: Uses real-time data to predict future costs and timelines more accurately.
- Reduces Risk: Identifies financial and schedule risks early so they can be tackled before they escalate.
- Optimizes Resources: Helps balance labor, materials, and equipment to maximize efficiency.
For example, if a contractor underestimates labor costs in the budget, the variance analysis process highlights the discrepancy before it turns into a funding shortfall. The project team can then reallocate resources, adjust forecasts, or negotiate subcontractor rates before costs spiral out of control.
Mastt makes this process easy with automated cost tracking and real-time financial dashboards, giving teams full visibility over budget variances without manual calculations.
What Causes Variances?
So, why do variances happen in projects? A perfect project management plan rarely exists because unpredictable factors always come into play. Some are unavoidable, while others stem from poor planning or mismanagement. The table below will outline these variance causes:
How Is Variance Calculated?
Numbers don’t lie. Variance analysis relies on specific formulas to measure how well (or poorly) a project is performing financially and time-wise.
Cost Variance (CV)
The cost variance helps determine if a project is staying within its budget. Are we over budget or under budget? Here's the formula for calculating Cost Variance CV:
CV = Earned Value (EV) - Actual Cost (AC)
- CV > 0: Under budget (good) - spending less than planned for work completed
- CV < 0: Over budget (bad) - spending more than planned for work completed
Schedule Variance (SV)
The schedule variance tells us if work is progressing on time. Are we ahead or behind schedule? Here's the formula for calculating Schedule Variance SV:
SV = Earned Value (EV) - Planned Value (PV)
- SV > 0: Ahead of schedule (good) - completed more work than planned
- SV < 0: Behind schedule (bad) - completed less work than planned
Variance at Completion (VAC)
The variance at completion predicts the budget status at project end. Will we exceed our budget by completion? Here's the formula for calculating VAC:
VAC = Budget at Completion (BAC) - Estimate at Completion (EAC)
- VAC > 0: Under final budget projection
- VAC < 0: Over final budget projection - needs corrective action
Let’s have an example calculation: If a project’s earned value (EV) is $1.2 million, but the actual cost (AC) is $1.5 million, the cost variance (CV) is -$300,000. That means the project is $300K over budget—a problem that needs immediate attention.
Reporting Variance in Project Management: Step-by-Step Guide
A variance report is a tool project managers use to compare planned vs. actual performance in a project. It highlights where things went off track—whether in cost, schedule, or resource allocation—so teams can fix issues before they spiral out of control.
A good variance report doesn’t just state the problem; it explains why it happened and what to do next. Here’s how to create a variance report:
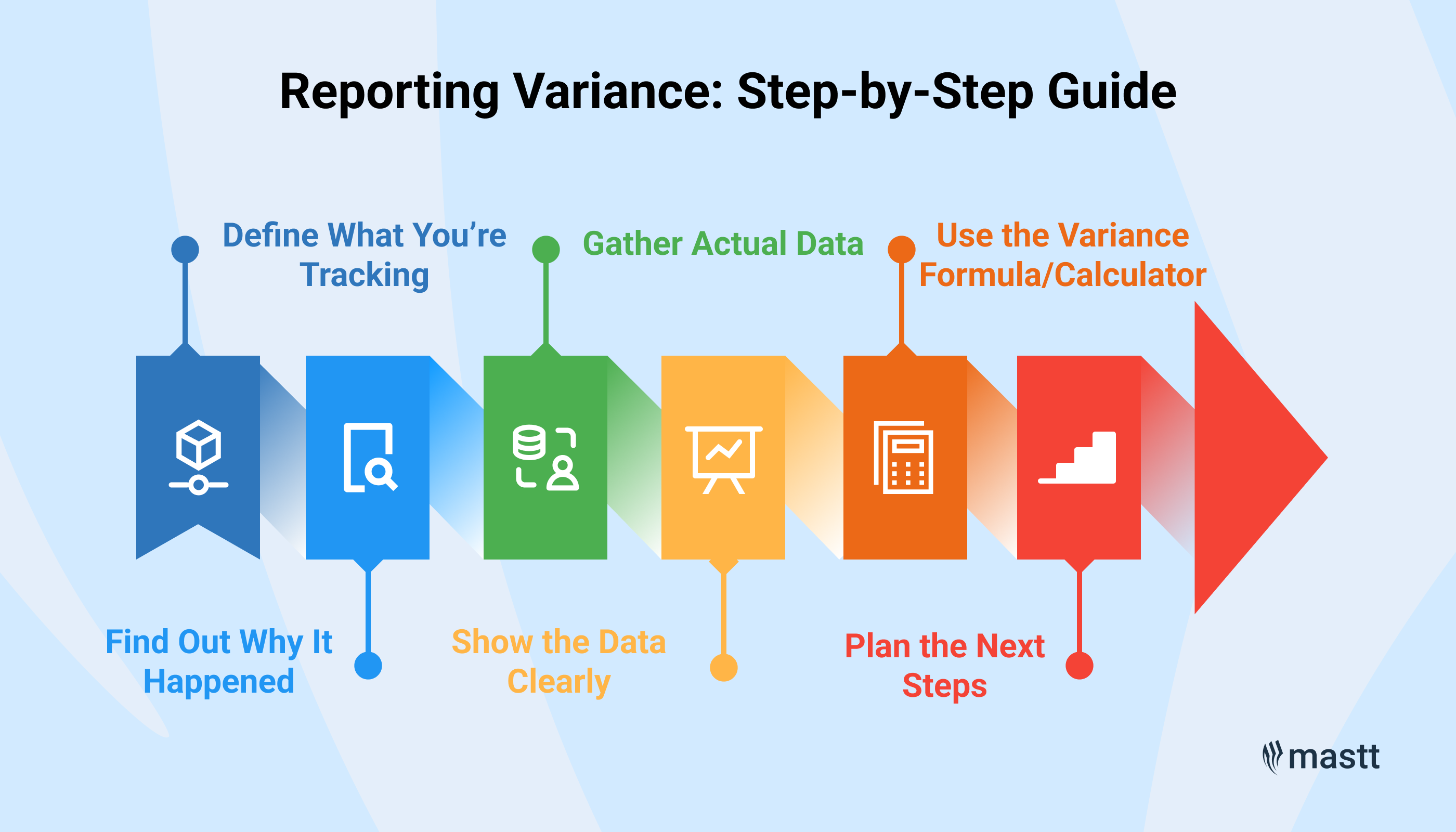
Step 1: Define What You’re Tracking
Decide what variances matter most. Cost variance (CV), schedule variance (SV), and resource variance are the big ones, but depending on your project, you might track quality or productivity gaps too.
Step 2: Gather Actual Data
Pull in real numbers—costs spent, work completed, hours used—and compare them to the original plan. If you're using project cost management software, it likely automates a lot of this.
Step 3: Use the Variance Formula or a Variance Calculator
If you want to calculate variance manually, use formulas like:
Calculate the variance using the formula I gave you earlier. Or, if you prefer a faster, easier way, use the variance calculator I shared to plug in your numbers and get instant results.
Step 4: Find Out Why It Happened
Numbers tell you what changed, but you need to figure out why. Was it unexpected price hikes? Labor shortages? Design changes? Digging into the root cause helps prevent the same issue next time.
Step 5: Show the Data Clearly
No one wants to read a wall of numbers. Use charts, graphs, and tables to show trends. A simple visual can tell your team more than a 10-page report.
Step 6: Plan the Next Steps
A variance report isn’t just about pointing out issues—it’s about fixing them. Propose corrective actions, like reallocating resources, renegotiating supplier contracts, or adjusting schedules to get back on track.
A solid variance report keeps projects predictable, budgets in check, and stakeholders informed. The earlier you spot and report variances, the easier it is to course-correct before small issues become major setbacks.
How to Track and Control Variance?
Tracking and controlling variance ensures projects stay within budget and on schedule. It involves continuously comparing planned costs and progress against actual performance to detect and resolve discrepancies to avoid cost escalation.
Here are simple steps to effectively track and control variance:
- Compare Planned vs. Actual Costs
- Regularly review cost reports to spot overruns early.
- Identify specific cost categories exceeding the budget.
- Monitor Work Progress Against Milestones
- Track project completion rates against the original schedule.
- Flag delays in procurement, labor, or subcontractor performance.
- Analyze Cost and Schedule Variances
- Use Earned Value Management (EVM) metrics like Cost Variance (CV) and Schedule Variance (SV).
- Determine if variances stem from inefficiencies, design changes, or unexpected site issues.
- Implement Corrective Actions
- Adjust work sequencing or reallocate resources to address delays.
- Renegotiate contracts or source alternative materials to control costs.
- Use Automated Tracking Tools
- Digital platforms provide real-time variance analysis, reducing reliance on manual spreadsheets.
- Automated alerts highlight budget or schedule deviations before they become critical.
With Mastt’s real-time cost tracking and automated reporting, project teams can quickly identify and respond to variances before they escalate. Its intuitive dashboards provide instant visibility into financial and schedule deviations, allowing for data-driven decision-making that keeps projects on track.
What Is the Role of Forecasting in Variance Analysis in Construction?
Construction cost forecasting in variance analysis helps involved teams predict future financial and scheduling outcomes based on current project trends. It allows for proactive decision-making, ensuring projects remain aligned with budgetary and time constraints.
Here’s how forecasting strengthens variance analysis:
- Identifies Cost Trends: Recognizes patterns in material price fluctuations and labor costs.
- Predicts Schedule Delays: Forecasts potential bottlenecks in procurement and construction phases.
- Improves Resource Allocation: Ensures labor and materials are available when needed, preventing last-minute shortages.
- Enhances Budget Accuracy: Projects final costs based on real-time spending patterns.
For example, if historical cost data shows material price increases of 5% per quarter, budgeting and forecasting allow teams to factor in cost escalation and adjust budgets accordingly. This prevents unexpected financial strain and ensures more realistic cost planning throughout the project lifecycle.
Challenges in Managing Cost and Schedule Variances
Despite its benefits, variance analysis in construction presents several challenges that can impact project outcomes.
One of the biggest challenges in variance analysis is visibility—without real-time insights, project teams often struggle to detect cost or schedule deviations before they escalate. That’s where Mastt comes in.
Instead of relying on outdated spreadsheets or fragmented data, Mastt provides real-time tracking of cost and schedule variances, allowing teams to make informed adjustments before small issues become major setbacks.
Best Practices for Using Variance Analysis in Construction
To make variance analysis effective, project teams must follow structured methodologies that ensure accurate tracking, interpretation, and corrective action implementation.
- Set a Realistic Baseline: Define project budgets and timelines based on historical data and risk assessments. Establish clear cost and schedule targets to track deviations effectively.
- Use Automated Tracking: Leverage project budget tracking software to monitor real-time cost and schedule changes. This ensures continuous visibility into labor, material, and progress updates.
- Review Variances Regularly: Conduct weekly or monthly variance reviews with key stakeholders. Identifying trends early helps maintain accountability and prevent budget overruns.
- Implement Corrective Actions: Address cost overruns by optimizing procurement and renegotiating contracts. Resolve schedule delays through re-sequencing tasks or allocating additional resources.
- Integrate with Risk Management: Align variance tracking with risk assessments to predict potential cost and schedule issues. Allocate contingency funds to high-risk areas to mitigate financial impact.
By following these best practices, project managers, contractors, and financial stakeholders can maximize cost control, improve project predictability, and enhance financial decision-making.
Let Mastt Help You With Variance Analysis Now!
Mastt’s construction project management software simplifies variance analysis by providing real-time financial tracking, risk management, and automated reporting tools.
Here’s how Mastt can support your project variance tracking:
- Comprehensive Cost Overview: Centralizes budgets, forecasts, variations, and payment data for full financial visibility.
- Real-Time Tracking: Updates cost and schedule metrics in real-time, reducing data discrepancies.
- Automated Reporting: Generates variance reports and dashboards instantly, replacing manual spreadsheets.
- Risk Management Integration: Links variance tracking with risk mitigation strategies, allowing project teams to proactively address potential overruns.
With Mastt’s data-driven approach, project teams can stay ahead of construction cost and schedule variances, improve financial decision-making, and enhance overall project efficiency.
After all, proactive variance analysis is one of the keys to delivering results for construction projects aiming for cost efficiency and operational success.