Anyone in construction knows the frustration of dealing with variations. They throw off schedules, inflate costs, and create conflicts that no one wants to deal with.
That’s why understanding the causes of variation in construction is crucial. Once you grasp why variations happen, you can reduce their impact significantly.
Let’s look at 10 common causes of variation in construction and how to avoid them.
1. Design Changes
Design changes are one of the biggest culprits behind project delays and budget blowouts. Sometimes, plans aren’t detailed enough from the start. Other times, a client rethinks their choices midway through construction. Either way, these changes can throw everything off track and often require a variation order.
Example
A commercial building project is moving along smoothly when the client decides they want a more high-end finish—swapping out standard tiles for premium marble flooring. The problem? The new material has a longer lead time and requires specialized installation. Suddenly, the flooring crew has to wait, the project timeline stretches, and costs climb.
How to Avoid This?
- Lock in designs early by getting all stakeholders to review and approve plans before construction begins.
- Use Building Information Modeling (BIM) to visualize the project in detail and catch potential conflicts ahead of time.
- Set clear expectations with clients about how changes will impact the budget and timeline.
2. Incomplete or Ambiguous Contract Documents
A well-structured contract sets the foundation for a smooth project. But when contract documents are incomplete, unclear, or poorly written, they leave too much room for interpretation. Contractors, subcontractors, and suppliers may all have different understandings of what’s required.
An analysis of road construction contracts in Australia found that contract variations added an average of 9.9% to the original contract value. Poorly defined contracts are one of the main drivers of these variations, leading to disputes and unplanned cost increases.
Example
A contractor is hired to build a mixed-use development, but the contract only vaguely specifies “high-quality finishes” without defining exact materials or standards. Midway through construction, the client insists that high-quality means Italian marble countertops, while the contractor had budgeted for quartz. Since the contract didn’t clarify this detail, both parties now face a costly dispute over who should cover the additional expense.
How to Avoid This?
- Be as specific as possible in contracts, defining materials, construction methods, and performance expectations clearly.
- Use contract reviews to ensure legal teams and technical experts validate the scope, responsibilities, and risk allocations before signing.
- Include a dispute resolution mechanism to handle ambiguities without stalling the entire project.
3. Unforeseen Site Conditions
No matter how well a project is planned, the ground beneath it can hold surprises. What looks like a perfect site on paper can turn into an expensive problem once excavation begins, sometimes requiring a variation request to cover additional work.
Common Unforeseen Site Conditions
- Unstable or Expansive Soil: Some soils, like clay, expand and contract with moisture changes, causing structural instability.
- Rock Layers or Hard Bedrock: Excavation can be significantly delayed if contractors unexpectedly hit solid rock that requires specialized removal equipment.
- Contaminated Soil: Industrial sites or old landfills may have hazardous materials that require environmental remediation before construction can proceed.
- High Water Table: If groundwater is closer to the surface than expected, foundation work may require additional drainage solutions or waterproofing measures.
- Buried Debris or Unknown Structures: Abandoned pipelines, old building foundations, or even historical artifacts can stop work until proper assessments and approvals are completed.
- Cavities or Sinkholes: Natural underground voids can lead to severe structural risks if not properly identified and reinforced.
- Utility Line Conflicts: Unknown or misidentified underground utilities (water, gas, electrical) can create delays and safety hazards.
- Poor Soil Bearing Capacity: If soil cannot support the intended load, deep foundations or alternative construction methods may be needed.
- Flood-Prone Areas: Some sites may not show obvious signs of flooding until heavy rain occurs, requiring additional drainage or site elevation adjustments.
- Seismic or Geotechnical Hazards: Some locations may have higher risks of earthquakes or landslides that require extra reinforcement in structural designs.
How to Avoid This?
- Conduct thorough geotechnical investigations before starting excavation to identify potential underground risks.
- Include contingency budgets in project estimates to account for unexpected site conditions.
- Negotiate contract clauses that allocate risk and responsibility for unforeseen conditions fairly between parties.
4. Documentation Errors & Poor Record Keeping
Even a small documentation error can create major project disruptions. Missing approvals, outdated drawings, or misplaced records can lead to rework, legal disputes, and cost overruns—ultimately reducing value for money.
Example
A subcontractor follows an old set of blueprints because the latest revisions weren’t properly communicated. As a result, they install ductwork in the wrong location, and the mistake isn’t caught until other trades have already built around it. The entire section must be torn down and redone, costing thousands in labor and materials.
How to Avoid This?
- Use cloud-based document management systems to ensure teams always have access to the latest approved plans.
- Implement strict version control so outdated drawings don’t get mistakenly used on-site.
- Schedule regular coordination meetings to keep all stakeholders aligned on project updates.
5. Client-Initiated Changes & Scope Creep
Clients often request changes once they see a project taking shape. While some adjustments are reasonable, excessive scope creep can send budgets spiraling and disrupt carefully planned schedules.
Example
A hotel is under construction when the client decides they want an additional rooftop bar. The problem? Structural reinforcements weren’t accounted for in the original plans, requiring expensive redesigns and significant delays to install additional supports.
How to Avoid This?
- Set clear expectations upfront by ensuring clients fully understand the project scope, timeline, and constraints before work begins.
- Use formal variation order processes that assess the cost and schedule impact of any requested modification before approval.
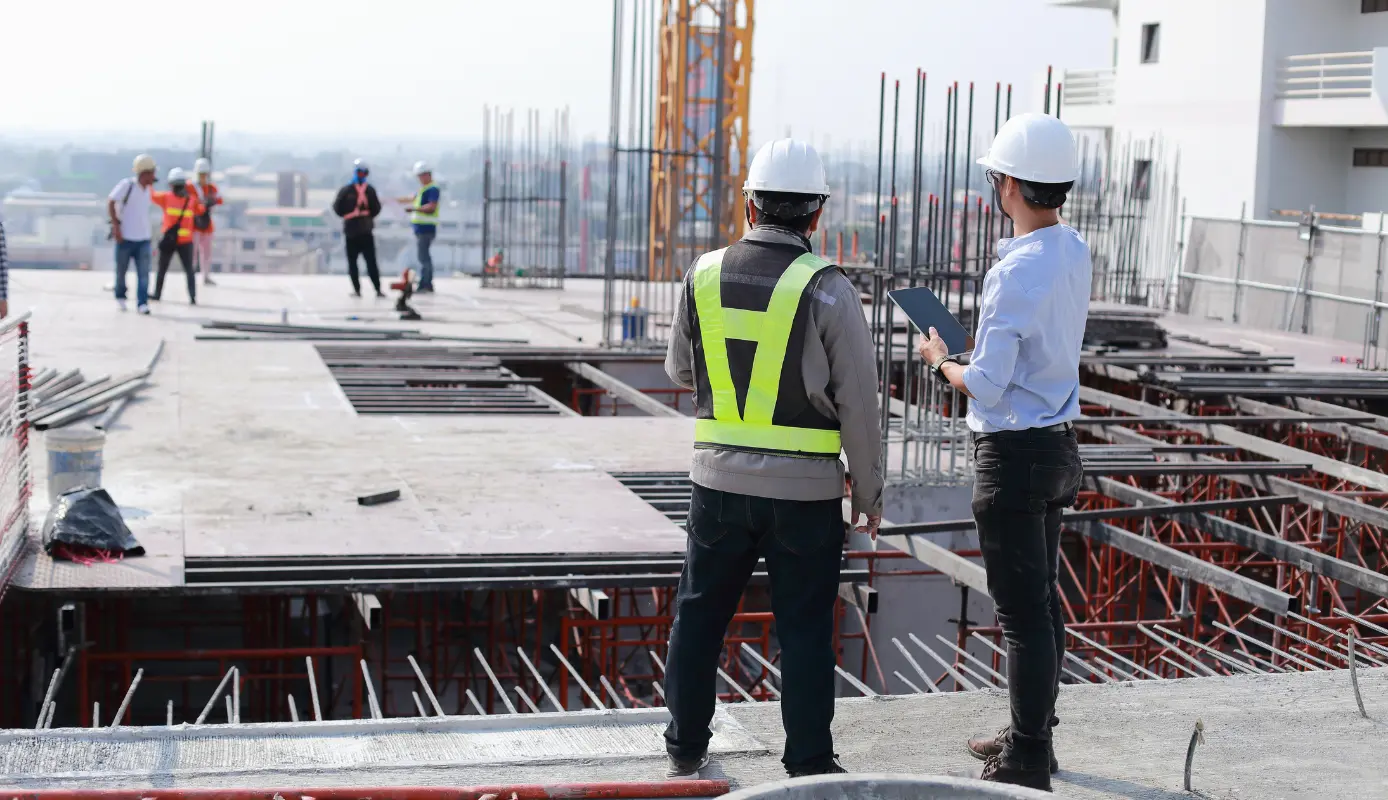
6. Inaccurate Cost Estimates & Budget Constraints
When project budgets are based on unrealistic estimates or outdated pricing, the entire financial structure of a job can collapse. Unexpected costs force project owners to scramble for additional funding, delay work, or cut corners.
Example
A government infrastructure project is greenlit based on a cost estimate from two years prior. By the time construction starts, material and labor costs have increased by 20%, leaving a funding shortfall that forces the project to halt midway while additional financing is arranged.
How to Avoid This?
- Use real-time market data to adjust cost estimates before finalizing budgets.
- Factor in material price escalation clauses in contracts to protect against inflation.
7. Delays in Approvals & Permits
Regulatory approvals can be a slow-moving process. When permits are delayed or rejected, entire projects can come to a standstill, leading to idle labor and financial penalties.
Example
A developer begins construction on a commercial complex, assuming that zoning approvals will be processed quickly. However, unexpected opposition from local authorities forces months of hearings and plan modifications. Construction crews sit idle, and the delayed start leads to contract penalties.
How to Avoid This?
- Engage with regulatory bodies early to understand potential permitting roadblocks.
- Hire permit expeditors who specialize in navigating complex approval processes.
8. Contractor & Subcontractor Issues
A project is only as strong as the contractors executing it. Poor workmanship, missed deadlines, or financial instability can disrupt schedules and create costly setbacks. If subcontractors fail to deliver quality work or abandon the job, the entire project can be thrown into chaos.
Example
A subcontractor responsible for electrical installations underbids the project to secure the contract but later realizes they can’t complete the work at the agreed price. Halfway through the job, they abandon the site, leaving the general contractor scrambling to find a replacement at a much higher cost.
How to Avoid This?
- Pre-qualify contractors based on financial stability, past performance, and references.
- Use performance bonds to protect against contractor defaults.
9. Material Shortages & Supply Chain Disruptions
Global supply chain disruptions, material shortages, and transportation delays can quickly throw a construction project off schedule.
Example
A high-rise developer sources specialty glass panels from overseas, assuming normal delivery timelines. However, unexpected port congestion causes a three-month shipping delay. This leaves the building’s exterior incomplete and delaying tenant occupancy.
How to Avoid This?
- Diversify suppliers to avoid reliance on a single source for critical materials.
- Stockpile key materials in advance when possible, especially for long-lead items.
10. Changes in Regulations & Compliance Requirements
Regulatory changes can disrupt projects if they require modifications to already approved designs or construction methods.
Example
Midway through a residential development, new fire safety codes require additional sprinkler systems in all units. The design must be altered, and the local fire department must reapprove the plans before construction can continue. The unexpected change leads to costly delays and material waste.
How to Avoid This?
- Monitor industry regulations closely to anticipate upcoming changes.
- Engage compliance consultants who specialize in local building codes.
Final Thoughts
Variations in construction often come from client changes, design adjustments, or unexpected site conditions, sometimes involving contractors. If not managed well, they can cause delays and cost overruns.
To reduce their impact, contracts should outline how variations will be handled. Planning for design changes, budget limits, material availability, and regulatory updates early on helps keep projects on track.