Life cycle cost analysis (LCCA) calculates the total cost of a project, including planning, building, maintenance, and disposal. It helps avoid budget overruns, reduce long-term costs, and make better financial decisions.
Want to do it right? This guide walks you through each step, so you can choose the most cost-effective option for your project.
What is Life Cycle Cost Analysis?
Life cycle cost analysis (LCCA) calculates the total cost of a project from start to finish. It includes all expenses related to planning, building, operation, maintenance, and disposal. The goal is to compare long-term costs and find the most cost-effective option.
To understand LCCA better, here are the cost factors it considers:
- Initial costs: Land, design, permits, and expenses.
- Operating costs: Energy, utilities, and labor required to run the facility.
- Maintenance and repair costs: Regular upkeep and unexpected repairs.
- Replacement costs: Upgrading materials, replacing equipment, or renovating.
- End-of-life costs: Demolition, waste disposal, or material recycling.
LCCA helps contractors, project owners, and planners avoid costly mistakes by showing the true financial impact of a project over time. For example, a low-cost material might seem like a good choice upfront but could lead to high maintenance and replacement costs later.
For practical tips on planning, tracking, and controlling your budget, check out our project cost management guide.
How to Make a Life Cycle Cost Analysis? (Step-by-Step Guide)
To make a life cycle cost analysis (LCCA), you need to calculate all costs of a project from start to finish and compare different options to find the most cost-effective choice. This involves listing expenses, estimating future costs, adjusting for inflation, and making an informed decision.
Below is a step-by-step guide that explains exactly how to do it.
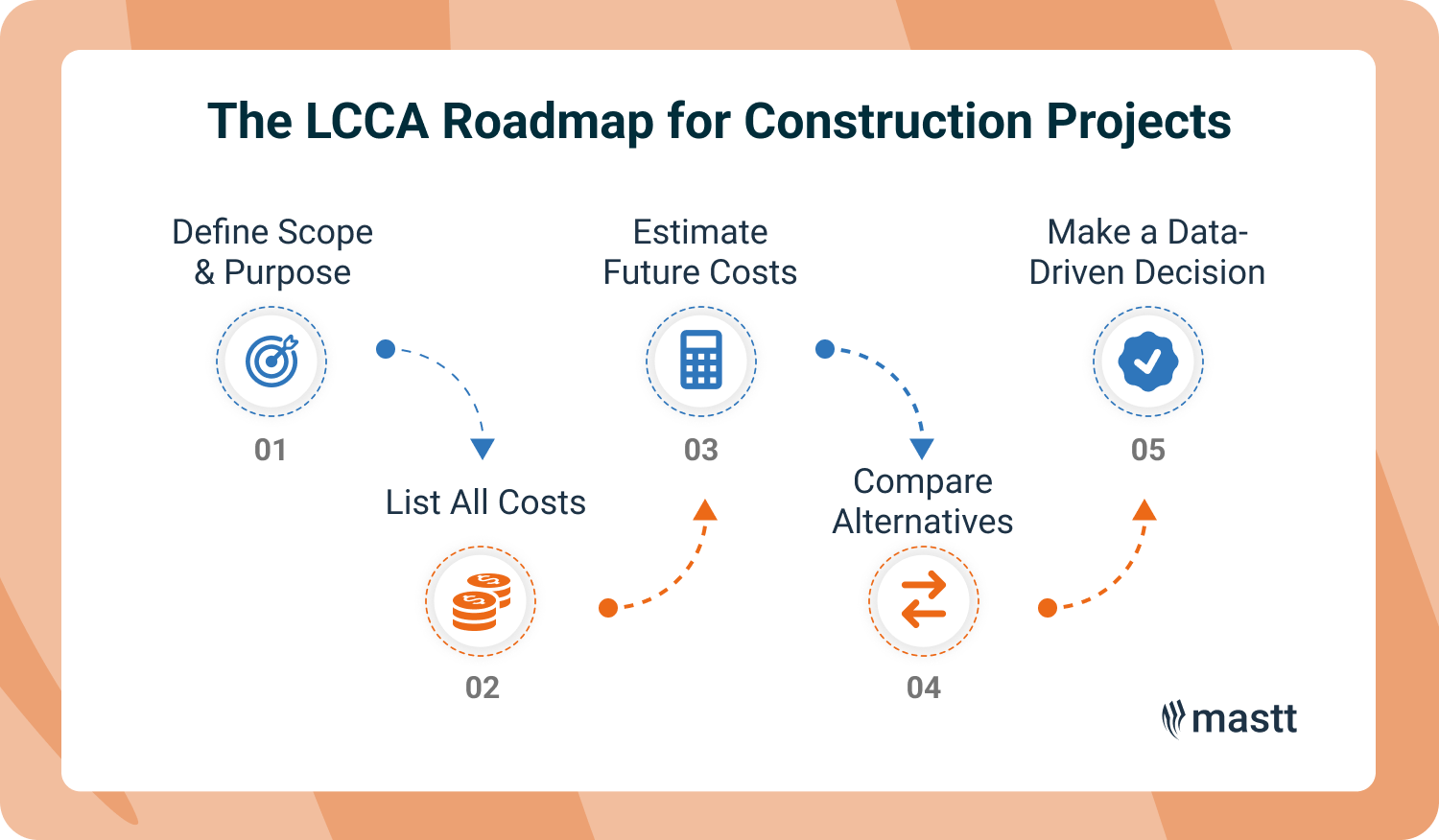
Step 1: Define the Scope and Purpose
Before starting, you need to clearly define what you are analyzing and why you are doing it. This step ensures that the analysis provides useful insights for decision-making.
How to Do It:
- Decide what to compare: Are you evaluating different building materials, construction methods, or energy systems?
- Set the time frame: Choose a useful life period (e.g., 10, 20, or 50 years) based on how long the asset is expected to last.
- List the cost factors: Include all expenses related to construction, operation, maintenance, and disposal.
- Select a financial method: Use calculations like Net Present Value (NPV) to measure long-term costs.
Step 2: Identify and List All Costs
To calculate the total life cycle cost of a project, you need to list all cost factors across its lifespan.
How to Do It:
Break down the costs into five main categories:
- Initial Costs: Land purchase, permits, design fees, materials, and labor.
- Operating Costs: Energy use, water bills, staff wages, and day-to-day expenses.
- Maintenance Costs: Regular servicing, cleaning, and minor repairs.
- Replacement Costs: Major upgrades, system replacements, and renovation expenses.
- End-of-Life Costs: Demolition, site clearance, and waste disposal.
Step 3: Estimate Future Costs and Adjust for Inflation
Since construction projects last for many years, future costs must be estimated and adjusted for inflation. This is important because money loses value over time, and materials, labor, and utility prices will likely rise.
How to Do It:
- Use historical data to predict future expenses for labor, materials, and energy use.
- Adjust for inflation using a discount rate, typically around 3-5% in construction projects.
- Convert future costs to today’s value using the Present Value (PV) formula: PV = Future Value / (1 + Discount Rate)ⁿ
Where:
- PV = Present Value (cost in today's money)
- FV = Future Value (estimated cost in the future)
- r = Discount rate (inflation-adjusted percentage)
- n = Number of years into the future
Example:
A project owner knows that replacing HVAC systems in an office building will cost $80,000 in 15 years. Using a 3% discount rate, the present value of that expense is: PV = 80,000 / (1.03)¹⁵ = 49,551
This means that $80,000 in 15 years is worth $49,551 today. Adjusting future costs helps construction managers compare long-term expenses fairly with today’s costs.
Use our construction cost calculator to quickly estimate material, labor, and other project costs for better analysis.
Step 4: Compare Alternative Options
LCCA is used to compare different options and determine which one is the best long-term investment.
How to Do It:
- Compare building materials: A cheaper option may need frequent replacement, while a durable option may have lower lifetime costs.
- Evaluate energy systems: A solar energy system costs more upfront but can reduce electricity costs over 30 years.
- Analyze maintenance costs: Some structures require ongoing maintenance, while others are designed for minimal upkeep.
Example:
A construction company is choosing between traditional concrete pavement and permeable pavement for a city road.
- Traditional pavement costs $500,000 upfront but needs resurfacing every 10 years at $200,000.
- Permeable pavement costs $800,000 upfront but lasts 30 years without major repairs.
Comparing their total costs over the project’s lifespan will determine which is the better financial decision.
Step 5: Make a Data-Driven Decision
After listing all costs and comparing options, it is time to analyze the numbers and make a final choice.
How to Do It:
- Calculate Net Present Value (NPV) to compare the total cost of each alternative.
- Use the Payback Period formula to see how long it takes to recover an investment through cost savings: Payback Period = Initial Cost / Annual Savings
- Justify your choice with cost-benefit analysis and supporting documentation.
Example:
A project manager is evaluating two insulation systems for a commercial building.
- Standard insulation costs $40,000 upfront and leads to $10,000 in yearly energy costs.
- Energy-efficient insulation costs $60,000 upfront but reduces energy costs to $6,000 per year.
Using the payback period formula: (60,000 - 40,000) / (10,000 - 6,000) = 5 years
This means that after five years, the extra investment is recovered, and all savings beyond that are pure profit.
Life Cycle Cost Analysis Example
This highway project is a perfect life cycle cost analysis example showing how comparing total costs over 40 years reveals the best value. Though Alternative B costs $16.2M more upfront, it saves $6.1M overall by reducing maintenance and user delay costs.
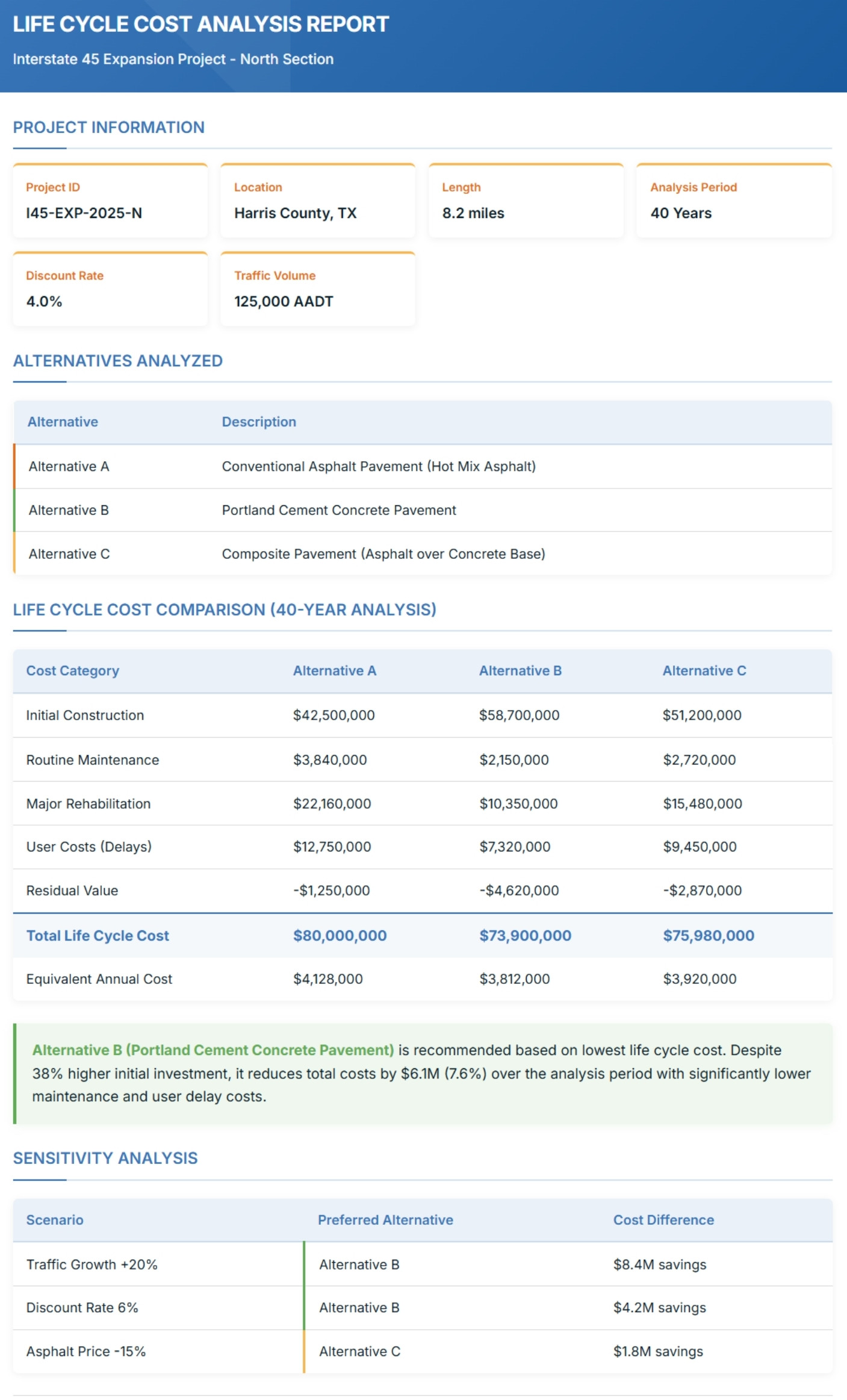
Who Should Use Life Cycle Cost Analysis?
Life Cycle Cost Analysis (LCCA) should be used by construction professionals responsible for budgeting, cost control, and long-term financial planning. Different professionals in construction apply LCCA for specific purposes:
- Project Owners & Developers: Calculate total project costs, including maintenance and future expenses.
- Contractors & Project Managers: Choose materials, equipment, and methods based on long-term cost efficiency.
- Government & Infrastructure Planners: Analyze public project investments by considering total ownership costs.
- Facility Managers: Plan for ongoing maintenance, repairs, and replacements to control long-term expenses.
- Sustainability Consultants: Compare the costs of energy-efficient materials and sustainable construction solutions.
LCCA is useful in both private and public construction projects. It provides a structured way to estimate costs, helping decision-makers plan effectively for the entire project lifecycle.
For more details on breaking down project expenses, visit our construction estimating guide.
When Should You Conduct a Life Cycle Cost Analysis?
Life Cycle Cost Analysis (LCCA) should be conducted before making financial decisions that affect a construction project’s long-term costs. It is best done at the start of a project to compare different options and choose the most cost-effective one.
LCCA is needed in these specific situations:
- Before finalizing project design: Helps compare different materials, construction methods, and building systems to find the lowest long-term cost.
- Before purchasing equipment or systems: Ensures that higher-quality, energy-efficient options are worth the investment compared to cheaper alternatives with higher operating costs.
- During budgeting and cost planning: Prevents cost overruns by estimating future maintenance, repair, and replacement costs early.
- Before renovating or upgrading a facility: Determines whether it is better to repair an existing system or replace it with a new one.
- When evaluating sustainability options: Assesses whether energy-efficient solutions, such as solar panels or insulation, provide long-term cost savings.
- Before starting public infrastructure projects: Helps governments and municipalities decide on the most cost-effective road, bridge, or public facility design.
LCCA should always be done as early as possible in project planning to prevent financial risks and unexpected costs. Waiting until later stages may limit options and lead to higher expenses in the future.
Tools & Methods for Life Cycle Cost Analysis in Construction
Life Cycle Cost Analysis (LCCA) requires the right tools and methods to calculate costs accurately and make informed decisions. Below is a breakdown of commonly used LCCA tools and how they help in cost planning.
🚀 Pro Tip: Stop guessing project costs! Mastt automates budget tracking, cost forecasting, and financial reporting—helping you stay on budget, reduce errors, and make smarter decisions.
Common Challenges in Life Cycle Cost Analysis & How to Solve Them
One of the biggest challenges in Life Cycle Cost Analysis (LCCA) is getting accurate cost estimates over a project's entire lifespan. Many construction professionals struggle with budget uncertainty, incomplete data, and complex financial calculations. Below are the most common LCCA challenges and how to solve them.
Budget Uncertainty
Material prices, labor costs, and inflation change over time, making future costs hard to predict. If budgets don’t account for these fluctuations, projects can face cost overruns.
✅ Solution: Use industry benchmarks, supplier data, and risk-adjusted pricing to create better cost estimates. Applying inflation rates and discount factors ensures more realistic financial planning.
Complex Financial Modeling
LCCA involves multiple calculations, including future costs, discount rates, and financial projections. Without the right tools, these calculations can be time-consuming and prone to errors.
✅ Solution: Automate financial modeling using LCCA tools and project cost management software. Platforms like Mastt help construction teams track costs, generate reports, and apply financial formulas like Net Present Value (NPV) and Discounted Cash Flow (DCF) to ensure accurate cost comparisons.
High Upfront Costs
Decision-makers often focus on lower initial costs instead of considering long-term savings. This leads to choosing cheaper materials or systems that cost more to maintain.
✅ Solution: Justify higher upfront costs by using payback period calculations and cost-benefit analysis. Showing how durable materials or energy-efficient systems reduce expenses over time can help secure better investment decisions.
Incomplete Cost Data
Many LCCA reports miss important costs like maintenance, repair, and end-of-life disposal. Ignoring these expenses leads to underestimating total project costs.
✅ Solution: Use historical project data and supplier estimates to identify all cost factors. Platforms like Mastt can centralize cost records, making it easier to track expenses and avoid missing critical financial data.
Difficulty Comparing Alternatives
Some materials and systems have different cost structures, making it hard to compare options. One option may be cheaper to install but expensive to maintain, while another may have a high upfront cost but lower lifetime expenses.
✅ Solution: Use financial methods like NPV and DCF to compare total life cycle costs. Standardizing cost evaluations ensures a fair comparison between alternatives.
Manual Data Entry Errors
Manually entering cost data can cause errors, miscalculations, and incorrect financial projections. Even small mistakes can create major budgeting problems.
✅ Solution: Use automated construction cost tracking software to minimize errors and keep financial data up to date. Digital platforms like Mastt help construction teams track project expenses in real time, reducing human errors and improving cost accuracy.
Key Takeaways for Effective Life Cycle Cost Analysis
Life Cycle Cost Analysis (LCCA) helps contractors, developers, and project owners make smarter financial decisions by considering long-term costs, not just upfront expenses. Accurate budgeting, cost tracking, and realistic projections prevent unexpected financial risks.
Using reliable data, comparing options fairly, and automating calculations improve accuracy and efficiency. When applied correctly, LCCA ensures better cost control, maximizes project value, and supports long-term financial sustainability.