Cost overrun happens when a project costs more than planned, causing budget issues and financial stress. It’s a common problem in construction, IT, and large infrastructure projects, often due to poor cost estimates, project delays, or unexpected price increases.
If not managed, cost overruns can drain funds, delay completion, and reduce profits. The good news? You can prevent them. In this guide, you’ll learn what cost overrun means, why it happens, and expert tips to keep your project budget under control.
What is a Cost Overrun?
A cost overrun happens when a project's actual cost exceeds the planned budget. This means spending more than expected, which can cause financial strain, project delays, or even project failure.
Cost overruns are common in construction, IT, manufacturing, and public infrastructure projects, where unexpected costs can quickly increase. Here’s a clear breakdown of what a cost overrun means and why it happens in projects:
- Cost overrun meaning: When a project spends more money than originally estimated, leading to higher-than-planned expenses.
- Industries most affected: Large-scale projects in construction, infrastructure, software development, and manufacturing face cost overruns due to complexity, price changes, and unexpected issues.
- Difference between cost overrun and budget overrun: Cost overrun refers to specific tasks or project phases exceeding their estimated cost, while budget overrun means the entire project surpasses its total allocated budget.
- Common reasons why projects exceed costs: Poor cost estimation, inaccurate financial forecasting, project delays, rising material prices, and unexpected design or scope changes.
- How cost overruns impact projects: They can reduce profits, cause funding shortages, delay completion, increase financial risk, or force changes to project scope.
A cost overrun doesn’t always mean a project will fail, but it creates financial risks that must be managed carefully. Companies and project managers use contingency budgets, construction cost tracker, and risk management strategies to keep projects within budget and reduce unexpected costs.
Check out our project cost management guide to learn expert strategies for budgeting, tracking expenses, and keeping your project on budget.

6 Causes of Cost Overruns & How to Prevent Them
Cost overruns happen when a project spends more money than planned due to poor budgeting, unexpected price increases, project delays, or changes in scope. To keep costs under control, project managers must use accurate cost estimation, strong risk management, and real-time budget tracking to identify problems early.
Below are the biggest reasons why projects go over budget and how to stop them before they become a major issue.
1. Poor Cost Estimation & Planning Mistakes
Many cost overruns start with bad budgeting and inaccurate cost estimates. If a project begins with incorrect financial planning, expenses can quickly spiral out of control. Without a detailed cost breakdown, teams often underestimate labor, materials, and equipment costs, leading to unexpected financial shortfalls.
Why it happens:
- Budget estimates are based on guesswork, not real project data.
- Teams fail to include contingency funds, leaving no buffer for unexpected expenses.
- Incorrect labor, material, or equipment calculations lead to shortages and costly reorders.
How to prevent it:
- Use historical project data and professional cost estimation tools for accurate budgeting.
- Always include a contingency fund (10-20%) to cover unexpected costs.
- Get multiple quotes from suppliers and contractors to create a more realistic budget.
Accurate cost estimation requires continuous updates and adjustments. Instead of relying on early estimates alone, teams should review and refine budgets as the project progresses.
Use our construction cost calculator to get accurate project estimates and avoid unexpected budget overruns.
2. Scope Creep & Uncontrolled Project Changes
Scope creep happens when new tasks, features, or requirements are added to a project after work has started. Even small changes can increase costs, requiring more time, materials, or labor. If these changes are not managed properly, they can push projects beyond their original budget.
Why it happens:
- Clients or stakeholders request extra work that was not part of the original plan.
- There is no formal approval process for evaluating how changes affect costs.
- Poor initial planning leads to frequent design changes and material adjustments.
How to prevent it:
- Set clear project requirements and objectives before starting work.
- Use a formal change request process to evaluate how changes impact costs before approval.
- Educate stakeholders about budget limits and the financial risks of adding extra work.
Sometimes, adjustments are necessary to improve the project’s quality or meet new regulations. But ensure to evluate the financial impact of each change before approving it.
3. Project Delays & Unplanned Expenses
Every day a project is delayed, costs increase due to extra labor, equipment rentals, and material storage. Delays also create scheduling conflicts, forcing companies to pay more for last-minute adjustments. The longer a project takes, the higher the overall expenses will be.
Why it happens:
- Poor scheduling causes workflow interruptions, idle labor, and wasted resources.
- Material or equipment shortages slow down progress and require expensive reorders.
- Unforeseen weather conditions or site issues create unexpected work stoppages.
How to prevent it:
- Develop a realistic project schedule that accounts for potential delays.
- Secure materials and equipment early to avoid last-minute price spikes.
- Monitor progress daily to identify problems early and adjust plans as needed.
A buffer time should always be included in project schedules to absorb small delays. For major projects, using scheduling software like Primavera P6 or Microsoft Project helps track timelines, adjust deadlines, and improve efficiency. This prevents unnecessary cost overruns caused by poor time management.
4. Rising Material, Labor & Equipment Costs
Project budgets are often set months or years in advance, making them vulnerable to cost escalation. Inflation, supply chain disruptions, and market changes can drive up material, labor, and equipment costs, leading to budget overruns.
Why it happens:
- Inflation and supply shortages cause material prices to increase unexpectedly.
- Lack of skilled labor forces companies to pay higher wages to attract workers.
- Fuel and transportation costs make shipping materials more expensive than planned.
How to prevent it:
- Lock in fixed-price contracts with suppliers and subcontractors whenever possible.
- Consider alternative materials or suppliers if prices become too high.
- Work with trusted vendors who have stable pricing and reliable delivery schedules.
Another strategy is bulk purchasing. Buying materials in advance when prices are lower can help stabilize costs and prevent budget blowouts. This approach works well for long-term projects where price fluctuations are a major concern.
5. Poor Risk Management & No Contingency Plan
Unexpected problems are a part of every project, but many companies fail to plan for risks. Without a contingency budget, teams have no financial buffer to cover unexpected costs, leading to budget overruns. A strong risk management plan helps teams anticipate issues and take action before they become costly problems.
Why it happens:
- No risk assessment before starting the project.
- Unexpected issues like weather problems, supplier failures, or legal changes cause financial surprises.
- Overconfidence in initial cost estimates, ignoring real-world uncertainties.
How to prevent it:
- Conduct a risk assessment before the project starts to identify potential issues.
- Set aside a contingency fund (10-20%) to cover emergencies.
- Regularly review risk factors throughout the project and adjust plans accordingly.
Risk management helps you identify problems so you can create solutions in advance. Teams should develop “what-if” scenarios and establish action plans for potential risks before they happen.
6. Bad Communication & Leadership Issues
Poor communication between teams, stakeholders, and suppliers leads to misunderstandings, costly mistakes, and budget mismanagement. Without clear direction, teams waste time, make incorrect purchases, and fail to control expenses.
Why it happens:
- Lack of clear roles and responsibilities, causing confusion in decision-making.
- Misalignment between contractors, suppliers, and project managers, leading to unexpected costs.
- No real-time cost tracking, making it hard to identify budget problems early.
How to prevent it:
- Use project cost management software to track costs, deadlines, and communication.
- Hold regular budget meetings with teams to ensure everyone is on the same page.
- Provide clear updates to stakeholders so they understand financial limits and project goals.
Leadership training is often overlooked, but a well-trained project manager can reduce cost overruns significantly. Strong leadership ensures that decisions are made quickly, problems are solved efficiently, and teams work together to keep the project on budget.
Cost Overrun Examples & Lessons Learned
Many projects around the world have gone over budget, causing financial losses, delays, and management failures. One of the biggest examples is the Sydney Opera House, which went over budget by 1,300% due to design changes, poor planning, and cost underestimation.
The table below highlights major cost overrun cases, their causes, and what can be learned from them:
These cases prove that poor cost estimation, unexpected risks, and lack of financial control often lead to budget overruns. To prevent these issues, companies should use accurate budgeting and forecasting in project management, risk analysis, and real-time budget tracking.
How to Track & Manage Costs to Budget Overruns
Tracking and managing costs properly helps keep projects within budget and prevents financial problems. The best way to avoid overruns is to monitor expenses in real-time, adjust budgets when needed, and control spending at every stage. Below are the key steps to track and manage costs effectively from start to finish.
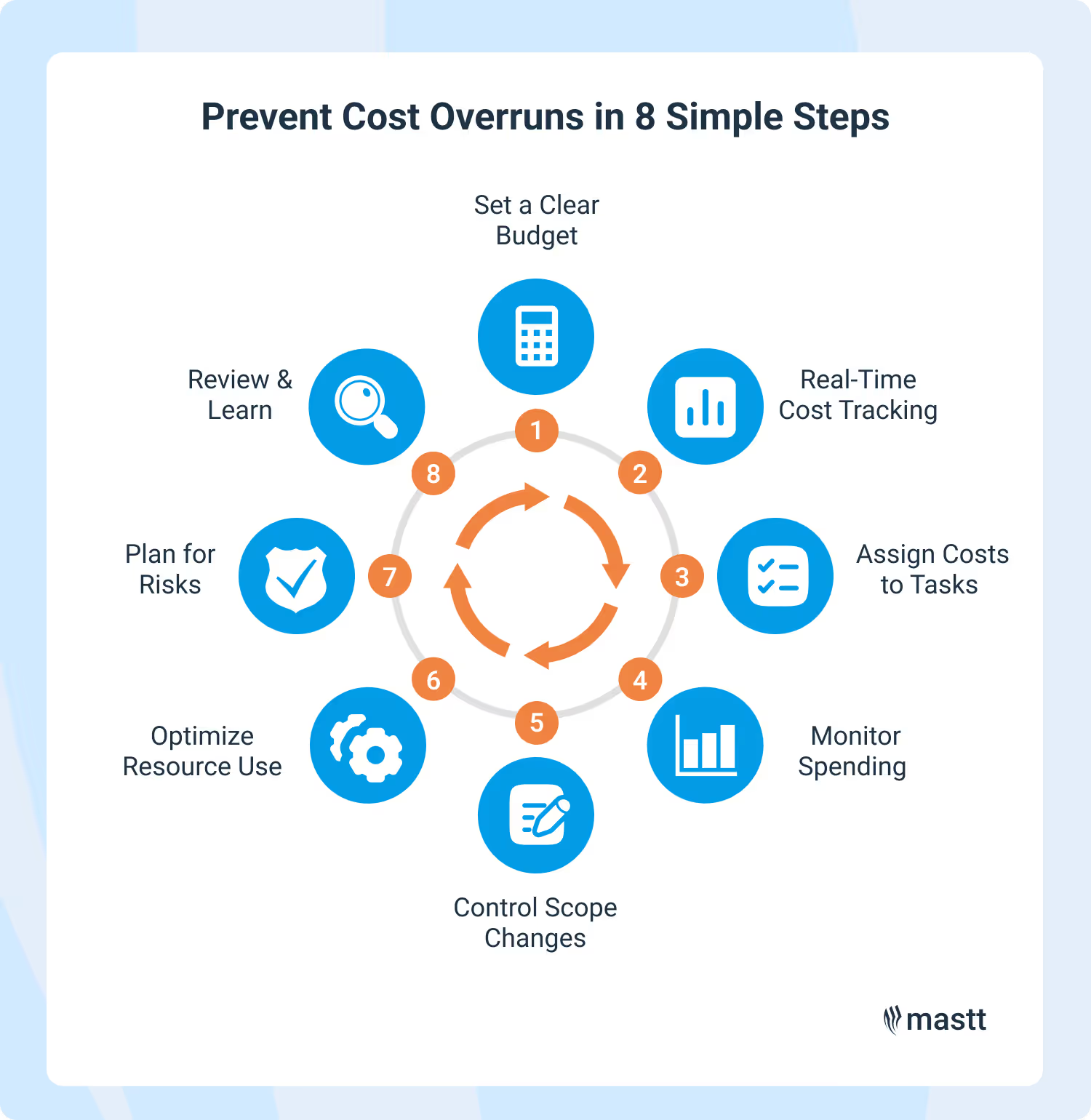
Step 1: Set a Clear and Detailed Budget
Create a realistic budget based on past projects, accurate cost estimates, and expert input. Include materials, labor, equipment, and contingency funds to cover unexpected costs.
Step 2: Use Real-Time Cost Tracking Software
Project costs change fast, so it's important to track expenses in real time. Using construction cost tracking software helps teams see where money is being spent and catch cost overruns early.
Step 3: Assign Costs to Specific Tasks
Break down your budget into detailed cost categories such as labor, materials, and subcontractors. This makes it easier to track spending and identify areas where costs are rising too fast.
Step 4: Monitor Spending Against the Budget
Regularly compare actual costs vs. planned costs to spot financial risks before they become a problem. Conduct weekly or monthly budget reviews with project teams to stay on track.
Step 5: Control Scope Changes and Approve Cost Adjustments
Every change in project scope affects the budget. Make sure all cost changes go through a formal approval process. This prevents unauthorized spending and keeps financial risks low.
Step 6: Optimize Resource Allocation
Assign the right people, equipment, and materials to tasks to avoid waste and delays. Poor resource management leads to extra costs from idle labor or equipment rental extensions.
Step 7: Plan for Cost Risks Before They Happen
Identify potential financial risks early and include a contingency fund (10-20%) in the budget. This way, unexpected expenses don’t disrupt the entire project.
Step 8: Review Project Costs After Completion
At the end of the project, analyze where costs went over budget and why. Use these insights to improve future cost management plan and avoid similar mistakes.
💡 Pro Tip: Mastt’s cost management tools track budgets in real time to control spending and prevent overruns. Stay on budget with smarter financial decisions! 🚀
Keep Your Projects on Budget Now!
Tracking costs early and making informed decisions keep projects financially stable. Every expense should have a purpose, and risks must be addressed before they turn into budget problems.
Struggling with cost overruns? Mastt makes budget tracking effortless with real-time project cost control and smart financial insights. Stay on track, cut waste, and deliver projects with confidence.