Managing construction projects is no small feat. With tight budgets, shifting schedules, and a thousand moving parts, it's easy for costs to spiral out of control. That’s where Project Cost Control comes into play. Mastering cost control is crucial for ensuring that projects are completed on time and within budget—without sacrificing quality.
What is Project Cost Control?
Project cost control is the process of monitoring and managing expenses throughout a project’s lifecycle to ensure you stay within budget. Sounds simple, right? Well, in construction, it’s anything but.
Imagine your project budget is a bucket of water. Every expense—materials, labor, equipment—is like a hole poked in that bucket. Cost control is the art of patching those holes before your budget leaks dry.
By closely monitoring expenses, you can identify potential overruns early, allowing for corrective action before costs spiral out of control. It’s like keeping an eye on your grocery bill while wandering through the aisles—there’s no shame in avoiding the snack section!
For a more in-depth look at cost management in construction, check out our Project Cost Management guide.
Why Is Cost Control Important in Construction?
Construction projects are notorious for cost overruns. According to a study by McKinsey, large projects typically exceed budgets by 20% and timelines by 80%. Yikes, right? Here’s why cost control in construction matters:
Unpredictable Costs
Material prices can fluctuate dramatically due to market conditions, transportation delays, or natural disasters. A delay in shipping steel, for example, might not only increase material costs but also extend timelines, leading to higher labor expenses.
Scope Creep
It’s not uncommon for clients to request changes during the construction process. Each change can lead to increased costs if not carefully managed.
External Factors
Weather delays, labor shortages, and regulatory changes can throw even the best-laid plans into disarray.
Without cost control, these challenges can snowball, turning a profitable project into a financial nightmare. Cost control isn’t just about preventing losses—it’s about driving efficiency and profitability.
Key Elements of Project Cost Control
For effective project cost control, it’s essential to integrate a few key elements into your project management approach. These foundational elements work together to ensure that your project remains financially healthy from start to finish:
Baseline Budget
The baseline budget is like your project’s financial game plan. It’s a detailed breakdown of how much money you plan to spend on everything—labor, materials, equipment, and even unexpected issues.
For example, let’s say you’re building a small office. Your baseline budget would list the cost of concrete, the wages for workers, the rent for equipment like cranes, and extra funds to cover things you didn’t plan for, like price increases for materials. This budget becomes the guide you’ll use to make sure you don’t overspend.
Cost Estimation
Cost estimation is figuring out how much each part of the project will cost before you start. You can use information from past projects, market trends, or advice from experts to come up with accurate numbers.
For instance, if you’ve built a similar office before and it cost $1,200 per square foot, you can use that number to estimate the cost of your new project. Of course, you’ll adjust it based on current material prices or changes in the scope of work.
Good construction estimating helps you avoid surprises and keeps your budget realistic.
Cost Tracking
Cost tracking is simply keeping an eye on what you’re spending as the project moves along. This is where tools like project cost control software come in handy. These tools show you how much money you’ve already spent and compare it to your budget.
For example, imagine you’ve budgeted $50,000 for materials, but halfway through the project, you see you’ve already spent $40,000. This lets you know you need to slow down spending in this area or find a way to cut costs.
Tracking your expenses regularly means you’ll notice problems early and have time to fix them. To learn more, see this project cost tracking guide.
Variance Analysis
Variance analysis is about checking if your actual spending matches your budget. If there’s a difference (called a variance), you figure out why.
Let’s say you budgeted $100,000 for labor, but you’ve spent $110,000. Why the extra $10,000? Maybe workers had to do overtime because materials were delayed. By identifying the problem, you can adjust your plan to avoid further overruns—like improving your schedule or finding a faster supplier.
This process helps you stay on top of your costs and prevent small issues from growing into big financial problems.
Cost Forecasting
Forecasting means looking at your current spending and predicting what future costs might be. It’s like looking ahead to see if you’re on track to finish the project within your budget.
For example, if you’re halfway through the project and you’ve already spent 60% of your budget, forecasting helps you figure out what adjustments you need to make. Maybe you need to cut costs in another area or speed up some tasks to avoid paying extra labor fees.
Forecasting keeps you ahead of potential problems and gives you time to fix them.
Reporting
Reporting is about keeping everyone involved—your team, your clients, and other stakeholders—up to date on how the project is going financially.
Good reports are clear and simple. They show:
- How much money has been spent so far.
- How much is left in the budget.
- Any differences between the budget and actual costs (like variances).
For example, if you’re running out of contingency funds faster than expected, a report can help explain why and start a conversation about adjustments. Regular updates build trust and keep everyone on the same page.
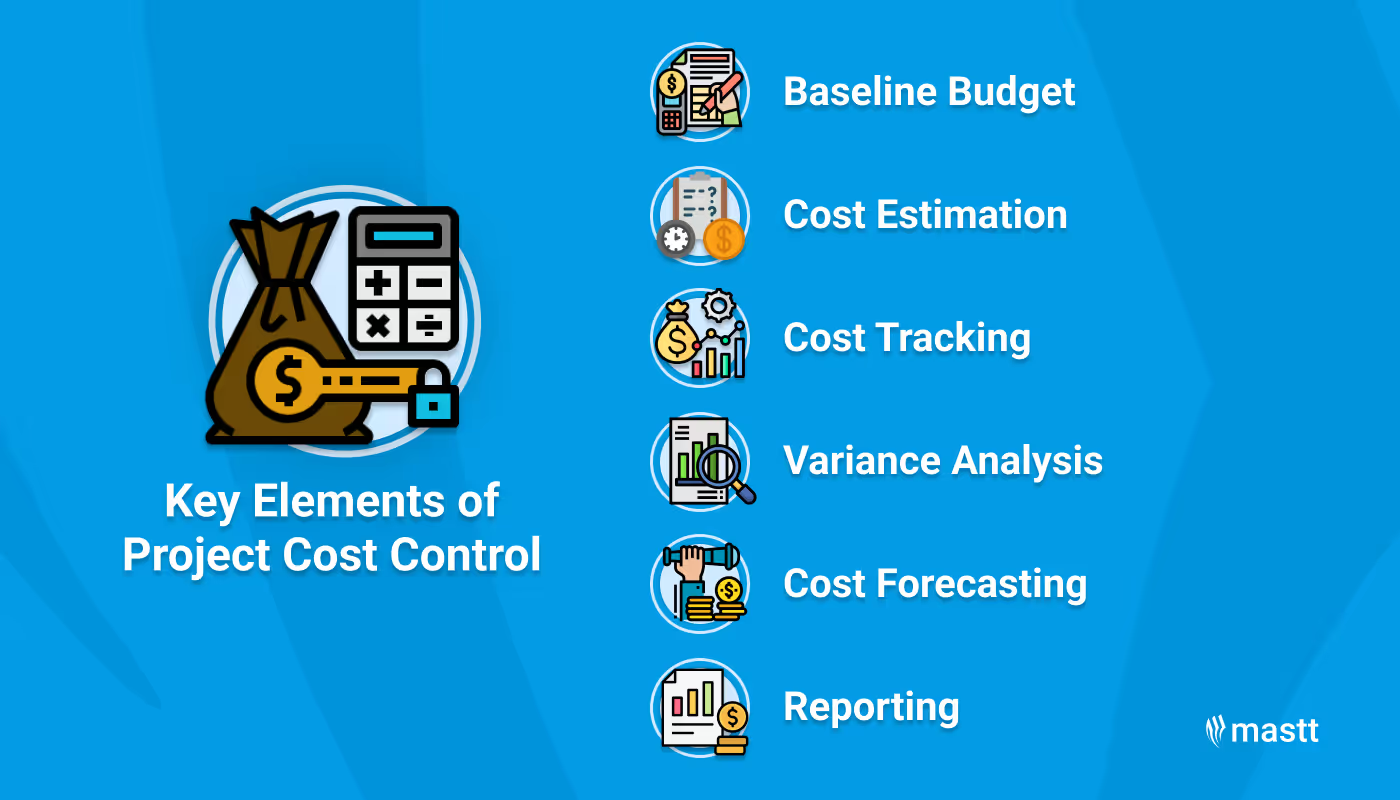
Best Practices for Cost Control in Construction
To manage costs effectively in construction projects, focusing on the most impactful strategies can make all the difference. Below are the five most critical practices to master project cost control:
1. Start with a Clear and Realistic Budget
Think of your budget as the game plan for your project. It should cover everything: labor, materials, equipment, permits, insurance, and even a cushion for unexpected expenses (usually 10–15% of the total). The more detailed your budget is, the fewer surprises you’ll face.
For example, if you’re building a commercial office space, don’t just budget for concrete and steel. Include the cost of site preparation, safety equipment, and potential delays. A clear budget sets the foundation for smooth project execution.
2. Monitor Your Costs Regularly
Keeping an eye on your spending is critical. Don’t wait until the end of the month to check your expenses—monitor them daily or weekly.
Use digital tools like dashboards or apps to track costs in real time. This way, you’ll spot problems early, like overspending on materials or unplanned overtime.
For instance, if you notice that your labor costs are creeping up, you can quickly adjust schedules or look for ways to cut back. Tools like Mastt’s project cost control software make this process simple by giving you instant updates.
For more ideas on staying on top of costs, check out Cost Schedule Control.
3. Keep Stakeholders in the Loop
Good communication is key to controlling costs. Regularly update your team, clients, and other stakeholders about the financial health of your project. Sharing updates—like whether you’re staying within budget or facing unexpected expenses—helps everyone make informed decisions together.
Let’s say your materials budget is running low because of a supplier delay. By sharing this information early, your team and clients can decide whether to adjust timelines or find alternative suppliers. Clear and open communication keeps everyone on the same page and builds trust.
4. Plan for Risks with a Backup Fund
Construction projects are full of surprises, from bad weather to rising material prices. That’s why it’s important to think ahead and set aside extra money—a contingency fund—for these unexpected costs.
For example, imagine you’re working on a residential project, and a sudden storm delays your work by two weeks. A contingency fund can cover extra labor costs or equipment rentals, so your project doesn’t grind to a halt. Planning for risks keeps your budget from taking a big hit.
5. Use Tools to Simplify Cost Management
Managing costs in spreadsheets manually is time-consuming and prone to errors. Instead, use tools like Mastt to track expenses, generate reports, and even predict future costs based on current trends.
For instance, if you’re juggling multiple projects, these tools can help you see all your expenses in one place, making it easier to spot problems or adjust budgets. They also save you time by automating repetitive tasks like generating cost reports.
What Are The Common Challenges in Cost Control
Even with the best strategies in place, construction project managers can fall into traps that lead to budget overruns and missed deadlines. Understanding these common mistakes and learning how to avoid them is key to mastering project cost control.
- Material Price Fluctuations: Prices for steel, concrete, and other essential materials can fluctuate, impacting project budgets.
- Design Changes: Mid-project design modifications can introduce new costs that weren’t accounted for in the original estimate.
- Labor Issues: Labor shortages or productivity delays can cause cost increases and impact timelines.
- Unexpected Site Conditions: Discovering unforeseen conditions like contaminated soil can lead to expensive remediation efforts.
Final Note
Mastering project cost control is essential for ensuring that construction projects stay within budget and are completed successfully. With the right processes, tools, and mindset, you can avoid cost overruns and keep your stakeholders happy. After all, no one likes an unexpected bill—especially when it’s in the millions!
(And remember, if things start to go sideways, don’t panic—there’s always value engineering to save the day!)