Ever been halfway through a construction project and realized the budget’s already out the window? It’s stressful, right? Unfortunately, this happens all the time—around 75% of construction projects go over budget. Why? Because cost forecasting wasn’t done properly.
But it doesn’t have to be that way. With the right approach, you can stay ahead of the curve, avoid nasty surprises, and keep your project on track. We’ll break down everything you need to know about cost forecasting—step by step. You’ll get simple tips, advanced techniques, and practical tools to help you nail your numbers and hit your KPIs.
What is Construction Cost Forecasting?
Construction cost forecasting is exactly what it sounds like: predicting the future project costs based on past and present financial data. It’s not just about making a good guess—it’s about using data, tools, and expertise to create an accurate estimate of what you’ll need to spend.
Forecasting plays a huge role in keeping your project on track. Without it, you’re flying blind, and unexpected costs can quickly derail everything. A solid forecast helps you plan better, make smarter decisions, and avoid unpleasant surprises along the way.
When done right, cost forecasting is a key part of project cost management. It protects important metrics like your budget variance (how much you go over or under budget) and profit margins. These numbers are critical for success, whether you’re managing a single project or overseeing a portfolio.
Why Forecasting Is Essential to Hitting Your KPIs
In construction, Key Performance Indicators (KPIs) often focus on time, cost, and quality. When it comes to cost-related KPIs, accurate forecasting is a game-changer. It helps you plan better, avoid budget overruns, and keep your stakeholders confident in your project’s success.
Think about it: if you’re not tracking and adjusting your expenses as new information comes in, you’re essentially guessing. And guessing doesn’t work when millions—or even billions—of dollars are on the line.
In fact, research shows that 70% of construction projects experience cost overruns, often because of poor planning and forecasting. That’s a big risk you can’t afford to take.
Here’s how accurate forecasting helps you hit your KPIs:
- Prevents Budget Overruns: By tracking expenses and updating forecasts, you can catch potential overruns before they spiral out of control.
- Improves Decision-Making: With reliable data, you can make informed adjustments as your project evolves.
- Boosts Stakeholder Confidence: Accurate forecasts show stakeholders that the project is on track, building trust and credibility.
- Supports Agile Project Management: Regular updates to your forecast keep your team proactive, not reactive.
The key to successful cost forecasting is continuous monitoring. As your project moves forward, compare your forecast with actual costs and adjust as needed. It’s not a “set it and forget it” process—it’s about staying agile and proactive. Missing a KPI due to a bad forecast? That’s like trying to hit a bullseye while blindfolded. You might get lucky once, but most of the time, you’ll miss.
Want to stay ahead of the curve? Check out cost control trends that are shaping the construction industry.
Steps to Effective Cost Forecasting in Construction
Getting construction cost forecasting right doesn’t have to be complicated. Follow these steps to build accurate forecasts and keep your projects on track:
Step 1. Gather Accurate Historical Data
Start by pulling data from past projects. Look for costs tied to similar tasks, materials, or timelines. This historical information gives you a solid starting point and makes your forecast more reliable. According to research by the Construction Industry Institute (CII), using accurate historical data can improve construction estimating accuracy by up to 20%.
Step 2. Set Realistic Budgets
Don’t fall into the trap of underestimating costs just to make the budget look good. It might save face initially, but it often leads to expensive problems later. Be honest about what your project will cost from the start. A realistic construction budget helps you manage expectations and avoids surprises. Remember, it’s better to explain higher costs upfront than to ask for more money halfway through.
Step 3. Incorporate Contingencies
No project goes exactly as planned—unexpected expenses happen. That’s why it’s critical to include a contingency reserve in your budget. Most experts recommend setting aside 5–15% of the total project cost for contingencies, depending on the complexity and risks involved. These reserves act as a safety net, ensuring you’re prepared for surprises without derailing the entire budget.
Want to learn more? Check out our guide on construction contingency for detailed tips.
Step 4. Regularly Review and Adjust Forecasts
Forecasts aren’t one-and-done—they need regular updates. As your project progresses, you’ll gather new information that impacts costs, such as material price changes or updated labor rates. Review and refine your forecasts often to keep them accurate. Research shows that projects with regular forecast reviews are 30% more likely to stay within budget (McKinsey, 2020).
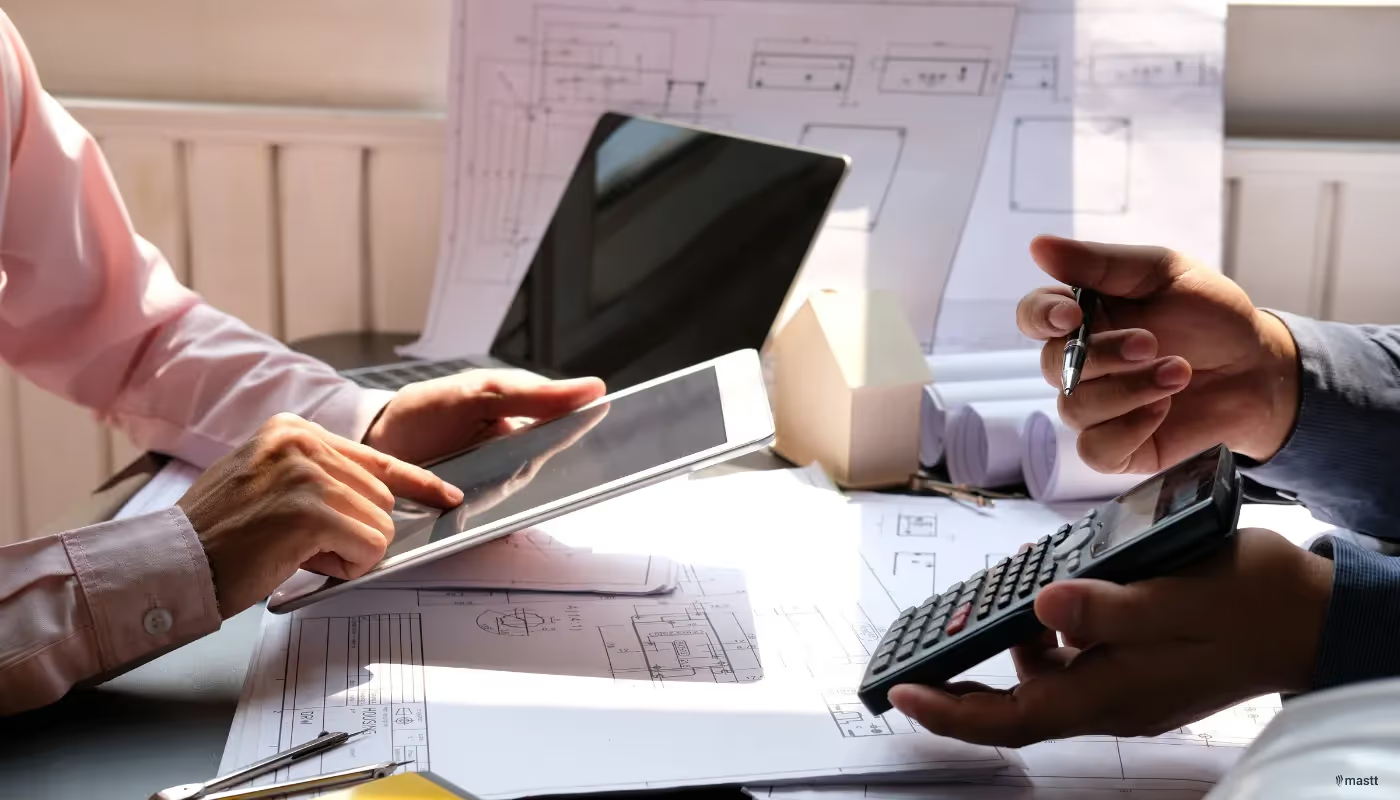
Forecasting Tools and Techniques
Gone are the days when construction managers relied solely on spreadsheets for cost forecasting in construction. Today, there are advanced tools designed to streamline the process and ensure accuracy.
1. Monte Carlo Simulations
Monte Carlo simulations might sound complicated, but they’re actually pretty straightforward. This technique runs a bunch of “what if” scenarios to show you different possible outcomes. Instead of guessing at a single project cost, you’ll get a range—like the best-case, worst-case, and most likely budgets.
For example, if you’re managing a large project with lots of unknowns, this method can show you the chances of staying on budget or where you might hit a snag. It’s a smart way to prepare for uncertainty and make more confident decisions.
2. Earned Value Management (EVM)
EVM is like a reality check for your project. It looks at what you planned to spend versus what you’ve actually spent and asks, “Are we on track?”
This technique is great for spotting budget problems early. If you’re overspending or not seeing the results you expected for the money spent, EVM will flag it. Over time, it helps you make better forecasts and avoid costly mistakes.
3. AI and Machine Learning Predictions
AI is no longer just for tech geeks—it’s transforming construction too. AI tools can analyze past project data, track current trends, and even factor in market conditions to predict costs with impressive accuracy.
For example, if your data shows that material prices usually spike during certain months, AI can adjust your forecast automatically
4. Project Management Software
Forecasting doesn’t have to feel overwhelming, especially with the right tools in your corner. Project management software like Mastt makes it easy to track costs in real time, automate reports, and manage budgets without the hassle.
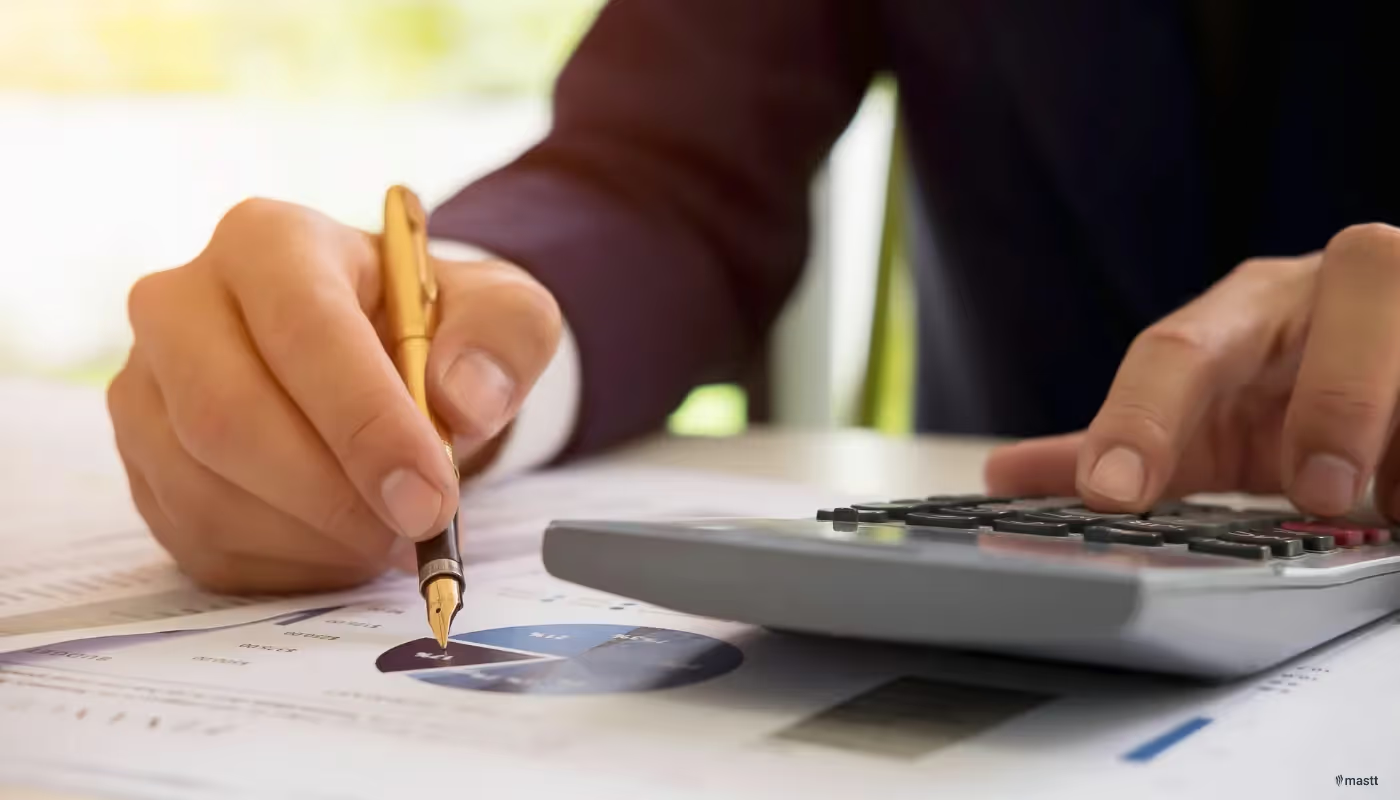
Common Challenges in Cost Forecasting
Even the best construction cost forecasting techniques can hit roadblocks. Knowing the common challenges upfront can help you avoid costly mistakes. Here’s what to watch out for and how to tackle them:
Unpredictable Market Conditions
The cost of materials and labor doesn’t stay the same for long. Prices can spike due to supply chain issues, seasonal demand, or economic shifts. If your forecast doesn’t account for these changes, you could be blindsided.
How to handle it: Stay on top of market trends by regularly reviewing reports and updates from reliable sources. Build flexibility into your forecast by including construction contingency reserves. For example, setting aside an extra 5–10% of your budget can help you cover unexpected cost increases without derailing your project.
Inaccurate Initial Estimates
Your forecast is only as good as the numbers it’s based on. If your initial cost estimates are wrong, everything else will be too. Common mistakes include underestimating material costs or overlooking labor hours.
How to handle it: Invest time in getting your initial estimates right. Use historical data from similar projects as a guide, and double-check your assumptions. Bringing in an experienced estimator or leveraging project management software can also help ensure your numbers are accurate from the start.
Poor Communication Among Teams
Forecasting isn’t a solo effort—it requires input from everyone involved in the project. But if your team isn’t sharing updates or is working in silos, critical details can fall through the cracks. This leads to surprises and errors in your forecasts.
How to handle it: Encourage regular communication between project managers, finance teams, and on-site workers. Weekly progress meetings can help ensure everyone is aligned. Tools like Mastt make it easier to centralize project data so that updates are automatically shared with the team.
Resistance to New Tools
Advanced forecasting techniques often require adopting new technology, but not everyone embraces change. Team members might resist using new software, preferring old-school methods that feel familiar but aren’t as effective.
How to handle it: Start by explaining the benefits of the new tools—how they save time, improve accuracy, and make life easier. Provide training to get everyone comfortable with the software. Choose user-friendly platforms, like Mastt, that simplify adoption and make the transition smoother.
Managing Stakeholder Expectations
Uncertainty is part of forecasting, but stakeholders often expect definitive answers. If you deliver overly optimistic numbers to keep them happy, it can backfire later when costs rise.
How to handle it: Be honest and transparent about the risks and assumptions in your forecast. Share potential scenarios, including best-case and worst-case outcomes, so stakeholders understand the full picture. This approach builds trust and avoids conflicts down the line.
Lessons From Poor Forecasting
A residential development in Melbourne faced major budget overruns due to poor forecasting. The initial estimates were rushed and didn’t account for fluctuating material costs or labor shortages. The project team also failed to update their forecasts as the project progressed, leaving them unprepared when unexpected expenses hit.
By the time they realized the issue, they were 20% over budget and weeks behind schedule. Stakeholders were frustrated, and the project’s profitability took a significant hit.
The lesson? Taking shortcuts with forecasting may save time upfront, but it often leads to bigger problems later. Accurate estimates, regular updates, and contingency planning are non-negotiable for keeping costs under control.
Final Thoughts
To hit your KPIs and stay within budget, construction cost forecasting is your best friend. With a combination of accurate data, solid management practices, and the right forecasting tools, you can steer your project to success—without unnecessary surprises. Remember, no one wants to explain why the budget exploded due to poor forecasting—save yourself the awkward meeting by staying on top of your costs.
And remember, forecasting is like a crystal ball for your project. Except, you know, way less magical but much more reliable!